Composites Design and Manufacture (Plymouth University teaching support materials)
Ceramic matrix composites - Metal matrix composites - Natural materials - Polymer matrix composites |
Lecture PowerPoint |
Review papers |
Subject Index |
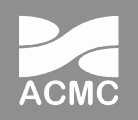 |
This schematic diagram indicates some of the extensive range of possible
composite materials. Composites can be broadly divided into:
Composite matrix |
Upper continuous operation temperature [Hancox & Phillips] |
polymer |
400°C |
metal (Al) |
580°C |
ceramic |
1000°C |
NL Hancox and DC Phillips, Fibre composites for intermediate and high temperature applications,
Proc 2nd Int Conf Materials Engineering, IMechE, London, November 1985, pp 139-144.
Key Texts
- B Cantor, F Dunne and I Stone, Metal and ceramic matrix composites,
Institute of Physics, Bristol, c2004. ISBN 0-7503-0872-9. PU CSH Library
- ST Mileiko - Metal and ceramic based composites, Elsevier, Amsterdam &
Oxford, 1997. ISBN 0-444-82814-1. PU CSH Library
- MR Winstone, A Partridge and JW Brooks -
The contribution of advanced high-temperature materials to future aero-engines,
Proceedings of the Institution of Mechanical Engineers - Part L: Journal of
Materials: Design & Applications, 2001, 215(2), p63-73.
CERAMIC MATRIX COMPOSITES
Carbon-carbon composites [Kelly]
Carbon fibre preform
- impregnated with char yielding organic liquid followed by pyrolysis:
phenolic or furfuryl resins, yielding ~55% carbon at 1000°C
liquid pitch and high isostatic pressure (70 MPa) yields ~85% carbon
- chemical
vapour deposition (CVD) of carbon from hydrocarbon precursor gas.
methane or natural gas under isothermal, thermal gradient or differential pressure conditions
Reference
- A Kelly, Concise Encyclopaedia of Composite Materials,
Pergamon Press, Oxford, 1989. ISBN 0-08-034718-5. PU CSH Library
Further reading
- KK Chawla, Ceramic matrix composites, Chapman & Hall, London, 1993. ISBN
0-412-36740-8.
- ER Generazio, Advanced ceramic matrix composites: design approaches,
testing, and life prediction methods, Technomic, 1996. ISBN 1-566-76334-7.
- Roger Naslain and Bryan Harris, Ceramic matrix composites: components,
preparation, microstructure and properties, Elsevier Applied Science, London,
1989. ISBN 1-85166-460-2. PU CSH Library
- R Warren, Ceramic-matrix composites, Blackie, 1992. ISBN 0-216-92682-3.
- SV Nair and K Jakus - High temperature mechanical behavior of ceramic
composites, Butterworth-Heinemann, Oxford, 1995. ISBN 0-7506-9399-1.
- AR Boccaccini, C Kaya and KK Chawla -
Use of
electrophoretic deposition in the processing of fibre reinforced ceramic and
glass matrix composites: a review, Composites Part A: Applied Science and
Manufacturing, 2001, 32(8), 997-1006.
- Zhihong Zheng and Dorel Feldman,
Synthetic
fibre-reinforced concrete, Progress in Polymer Science, 1995, 20(2),
185-210.
METAL MATRIX COMPOSITES
Unreinforced metal
FAST-forge is a novel cost-effective processing route using field assisted sintering technology (FAST) to consolidate titanium alloy powders into near net-shape components. The use of Spark Plasma Sintering (SPS) with a post-sinter forging process produces parts with wrought properties in just two steps.
FABRICATION PROCESSES for metal-matrix composites
LIQUID STATE: The generation of a metal matrix composite is primarily achieved by means of a liquid-metal
technique: either infiltration of a molten metal into fibre bundles or preforms
or the mixing of molten metal with reinforcement particles. The processing
occurs at high temperatures with the risk of chemical reactions.
Liquid pressure forming (LPF), including the Cray process [Ponzi]
Similar to RTM with molten metal fed into an evacuated fibre-filled mould from below by pressure.
Gases and volatile binders are vented from the mould top. Pressures are higher
(10-15 atm for Saffil preforms, 70 atm for 50 v/o carbon fibre). High clamping
loads, massive dies for heat retention, long solidification times.
Pressure infiltration casting (PIC), including PCAST process [Ponzi]
Similar to LPF except the mould is a cold thin walled vessel located inside and clamped by a pressure vessel.
Low cost tooling.
Squeeze casting [Ponzi]
High-quality casting by pressurising to 1000-2000 atm during solidification collapsing porosity and
increasing thermal contact with unheated die wall resulting in rapid
solidification rate. High capital facility and tooling costs.
Casting/semi-slurry technique [Ponzi]
Two phase process for (continuous) casting, limited to short-fibre/particulate reinforcement. Phase
1: dispersal of reinforcement in molten metal. Phase 2: shear dilution.
Produces ingots which can be subsequently reprocessed.
Osprey technique [Ponzi]
Liquid aluminium alloy atomised, and fed with 5μm (silicon carbide) particles, in nitrogen atmosphere sprayed onto collector surface.
SOLID STATE
Low temperature processes with diffusion bonding.
Foil techniques [Ponzi]
Compaction of fibre reinforcement within metal foil matrix below the solidus temperature. Some
interfacial reaction occurs. Typical forms include:
- foil plating by cold rolling
- explosion welding
- hot pressing (HP)
- hot isostatic pressing (HIP)
Powder techniques [Ponzi]
Aluminium alloy matrix materials canned and vacuum-degasses prior to consolidation to minimise surface oxidation and contamination
SECONDARY PROCESSING
Extrusion, forging, rolling, stamping, superplastic forming.
Machining [Taya & Arsenault]:
- superhard cutting and grinding tools
- AJM: abrasive waterjet cutting
- CHM: chemical milling
- EBM: electron beam machining
- EDM: electro-discharge machining
- LBM: laser beam machining
- PAM: plasma arc machining
- USM: ultrasonic machining
Resource
Further reading
- N Chawla and KK Chawla, Metal Matrix Composites, Springer, 2006. ISBN
0-387-23306-7. PU CSH Library
- TW Clyne and PJ Withers, Introduction to metal matrix composites,
Cambridge University Press, 1993. ISBN 0-521-41808-9.
- JN Fridlyander, Metal matrix composites, Chapman & Hall, London, 1995.
ISBN 0-412-58260-0.
- KA Lucas and H Clarke, Corrosion of aluminium-based metal matrix
composites, Wiley Research Studies Press, 1993. ISBN 0-471-94189-1. PU CSH Library.
- KU Kainer, Metal matrix composites: custom-made materials for automotive
and aerospace engineering, Wiley-VCH, Weinheim, c2006. ISBN 3-527-31360-5. PU CSH Library.
- AG Metcalfe, Composite materials volume 1, Interfaces in metal matrix
composites, Academic Press, New York & London, 1974. ISBN 0-12-136501-8. PU CSH Library.
- C Ponzi, Metal matrix composite fabrication processes for high performance aerospace structures,
Composites Manufacturing, 1992, 3(1) 32-42.
- WJ Renton, Hybrid and Select Metal Matrix Composites, American Institute
of Aeronautics and Astronautics (AIAA), New York, 1977.
- P Rohatgi, Microstructure formation during solidification of metal
matrix composites, TMS, USA, 1993. ISBN 0-873392-14-0. PU CSH Library
- JE Schoutens and K Tempo, Introduction to metal matrix composite
materials, Metal Matrix Composites Information Analysis Center, 1982. ISBN
0-6864-8246-8.
- M Taya and RJ Arsenault, Metal matrix composites: thermomechanical
behavior, Pergamon Press, 1989. ISBN 0-08-036983-9.
- B Terry and G Jones, Metal-matrix composites: current developments
and future trends in industrial research and applications, Elsevier Advanced
Technology, 1990. ISBN 1-85617-021-7. PU CSH Library
FUNCTIONALLY GRADED MATERIALS (FGM)
NATURAL MATERIALS
This topic is embedded throughout the module. Key pages include:
Since ancient times, man has used both plant- [1-5] and animal-based [6, 7] natural composite materials in a variety of ways. The Christian Bible makes an early reference to natural materials within composites (see the quotation below).
6 That same day Pharaoh gave this order to the slave drivers
and overseers in charge of the people. 7 “You are no longer to supply the people with straw for making bricks;
let them go and gather their own straw.
Exodus 5: 6-7 New International Version (NIV) |
Limpet teeth are formed by biomineralisation of goethite nanofibres in a soft natural polymer that acts as a framework for the formation of the reinforcement network. Asfa-Wossen [8] (quoting Asa Barber) states that limpet teeth "are more rigid and 10% stronger than spider silk ...[with] a tensile strength of 5 GPa" and were found to be stronger than most "engineering alloys, including ferrous and titanium alloys".
References
- KA Chowdhury, Wood and its use during pre- and proto-historic times, Indian Journal of the History of Science, 1970, 5(1), 141-143.
- R Meiggs, Trees and Timber in the Ancient Mediterranean World, Clarendon Press, Oxford, 1982.
- PI Kuniholm, Wood in EM Meyers (editor): The Oxford Encyclopedia of Archaeology in the Near East, Oxford University Press, New York, 1997, 347-349.
- P Fu, J Chapman and B Vale, Timber in Ancient China: wood work and wood processing as recorded in the ancient texts, NZ Timber Design Journal, 2004, 12(3), 3-10.
- Manfred Rösch, Forest, Wood, and Ancient Man, Interdisciplinaria Archaeologica/Natural Sciences in Archaeology, 2012, III(2), 247-255.
- A MacGregor, Skeletal materials: their structure, technology and utilisation c. A.D. 400-1200, Doctoral thesis, Durham University, 1980.
- A MacGregor, Bone, Antler, Ivory and Horn: the technology of skeletal materials since the Roman Period, Croom Helm, London. 1985. ISBN 0-7099-3242-1.
- L Asfa-Wossen, Limpet teeth bite back, Materials World, April 2016,2494), 33-35. Online access limited to IOM3 members.
POLYMER MATRIX COMPOSITES
This topic is the core interest of this module. The teaching support
materials can be accessed from the MATS 347 home page.
In tonnage terms, rubbers and elastomers are important matrix materials.
They find application in tyres, hoses, conveyor belts, sonar domes, etc.
Initially these material systems were reinforced with cotton then rayon or nylon
and latterly either steel or aramid, most often as cord reinforcement.
Further reading:
- John Loadman, Tears of the tree: the story of rubber-a modern marvel, Oxford University Press, Oxford & New York, c2005. ISBN 0198568401. PU CSH Library.
- D Boast and VA Coveney, Finite element analysis of elastomers, Professional Engineering Publications, Bury St Edmunds, 1999. ISBN 1860581714. PU CSH Library.
- WC Wake and DB Wootton, Textile reinforcement of elastomers, Applied
Science Publishers, London, c1982. ISBN 0-85334-998-3.
Return to MATS 347 home page
Created by John Summerscales on 18 October 2004 and updated on
06-Oct-2023 16:39. Terms and conditions. Errors and omissions. Corrections.