Composites Design and Manufacture: brief overviews
The manufacture of continuous fibre reinforced composites has been reviewed by a number of authors [1-12]. The International Standards ISO 12215 for small craft hull construction and scantlings define minimum requirements for materials, workshop and manufacturing and other arrangements. The majority of high-performance composite components manufactured rely on thermosetting matrix system processes as described below, with thermoplastic matrix system processes described at §7 below.
Thermosetting resins are small molecules with reactive sites. They are normally supplied as liquids and are cured (cross-linked to form a 3-D network) by the addition of chemicals (catalysts for unsaturated polyester and vinylester, or hardeners for epoxy resin). Faster processing can be achieved by the addition of accelerators and/or increased temperatures. The use of ultra-violet curing resin systems has been reviewed by Shukla et al [13]. The stages of cure are:
- A-stage: soluble and fusible (a.k.a. resol in phenolics). This stage is the normal form for liquid resin.
- B-stage: may be swollen, but not dissolved by a variety of solvents (a.k.a. resitol in phenolics). This stage is used in pre-impregnated (prepreg) reinforcements where the reaction is started before the fabric is impregnated, then the cure rate is reduced to almost zero by storage in a freezer (typically -20°C) until the reinforcement is required.
- C-stage: rigid, hard, insoluble, infusible (a.k.a resit in phenolics). This stage is the composite product.
1 Gel coating
Gel-coats are the outer aesthetic and corrosion-resistant surface of a laminate. It is normal practice to coat the mould tool with a gel-coat before commencing lamination, rather than painting the component after fabrication. The laminate is then manufactured, before the gel-coat has fully cured, and bonds to the gel-coat. During the gelling phase, volatile organic compounds (VOC), especially the styrene in unsaturated polyester or vinyl ester resins, escape into the workspace. Rogers et al [14] have reviewed the potential for in-mould gel-coating (IMGC) as a route to improved workplace conditions and reduced environmental impact. Di Tomasso et al [15] have demonstrated new IMGC processes that offer a reduction in average styrene emission levels of >98% (worst new/best old) with obvious benefits for worker health and the reduction of environmental burdens.
2 Contact moulding (hand lay-up and spray lamination)
For low performance components, spray (chopped fibres, Figure 1) and hand-lamination (all reinforcement forms) are often chosen because the raw materials are relatively inexpensive, the process uses relatively unskilled labour and the mould tools do not need to be vacuum tight.
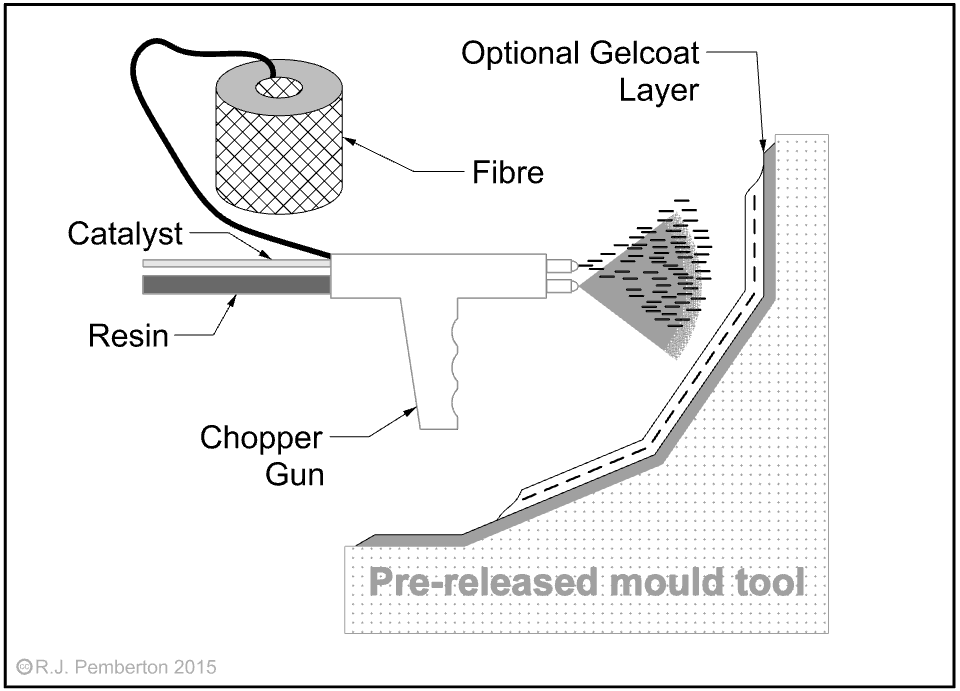
Figure 1*: Spray deposition
For hand lamination (often referred to as bucket-and-brush, Figure 2), the resin is introduced to the reinforcement by either stippling for continuous random swirl reinforcements or brushing for fabric reinforcements. A roller or “squeegee” may be used to thoroughly wet the reinforcement and encourage air bubbles to leave the laminate. They are often referred to as consolidation rollers, but there is little evidence that they cause a significant increase in fibre volume fraction. The laminates normally cure under standard workshop ambient conditions. However, these open mould processes produce composites with low fibre volume fractions and high levels of voids and/or porosity. Nevertheless, statistics from the National Boat Show indicated an “increase from 4% to 80% between 1955 and 1972 in the proportion of boat hulls constructed in GRP [16, 17].
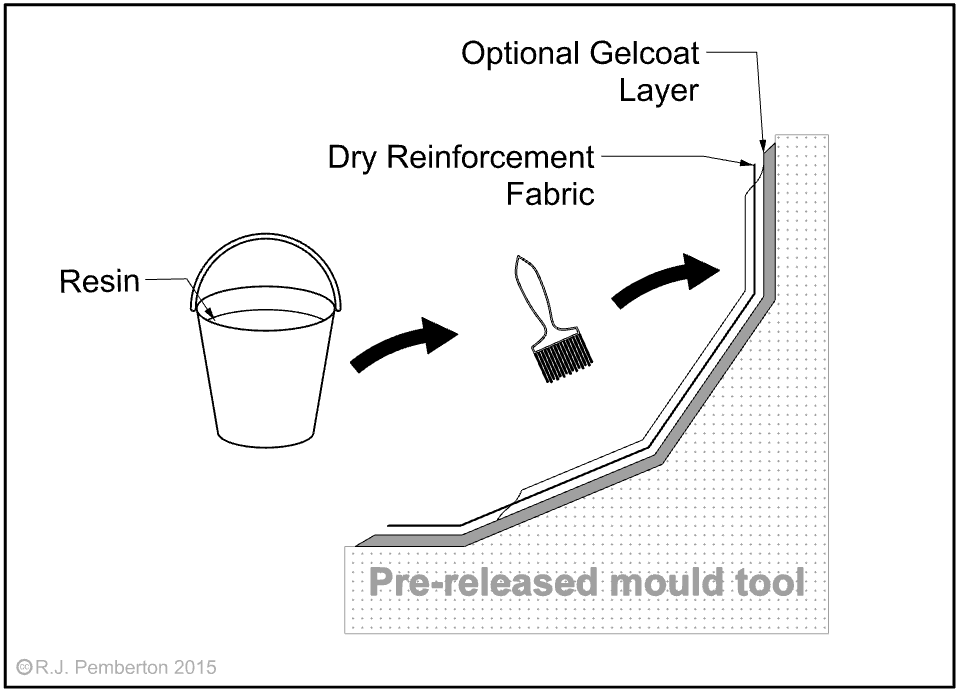
Figure 2*: Hand lamination
3 Vacuum bagging (VB), autoclave and compression moulding
For higher-performance composites, wet-lay-up or pre-impregnated (prepreg) materials can be enclosed in a vacuum bag and when the bag is evacuated, up to one bar of consolidation pressure is applied. Wet lay-up with a multi-part resin system leaves the composite manufacturer open to errors in measurement and mixing. For prepregs, the mixing is the responsibility of the prepreg materials supplier. It is essential (a) to allow the prepreg to rise to ambient temperature before laminating to minimise moisture entrapment in the laminate, and (b) to respect the prepreg manufacturers recommendations for “shelf-life” (time in the freezer) and “out-life” (time out of the freezer for part cutting and kitting) especially when manufacturing safety critical structures.
For even higher performance, further external consolidation pressure can be applied to the bag in an autoclave [18-23]. Autoclave pressures might be up to 7 bar for thermosets or 14 bar for thermoplastics. Louis and Ermanni [24] and Centea et al [25] have recently published reviews of out-of-autoclave prepregs and their processing. Components can also be manufactured by compression moulding between matched tools in a press [26, 27].
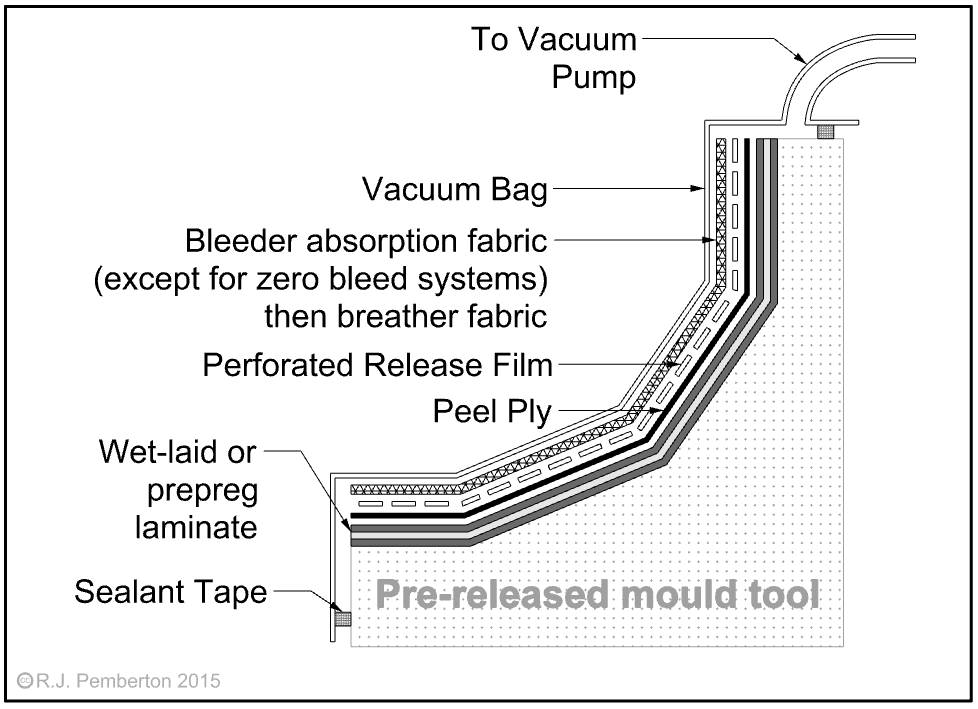
Figure 3*: Vacuum bagging for cure in oven or autoclave
There is increasing interest in out-of-autoclave (OOA) processes, including vacuum bag-only (VBO) prepreg and resin infusion, to reduce manufacturing costs and cycle times.
4 Liquid composite moulding (RTM and RIFT)
Liquid Composite Moulding technologies, especially Resin Transfer Moulding (RTM) [28-26] have emerged as the most probable route to mass production for small-medium sized composite components of complex shape. In RTM, a two- (or more) part mould is loaded with dry fibres, then resin flows into the fabric stack, before the resin cures to produce a solid component. While RTM is appropriate for relatively small components, the mould closure forces become excessive as component size increases.
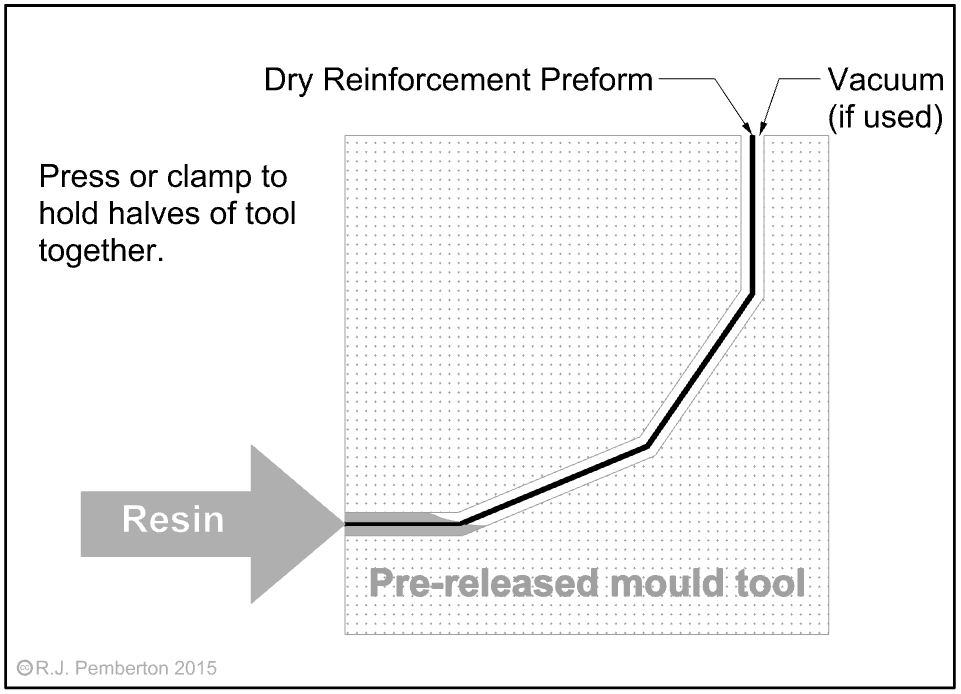
Figure 4*: Resin transfer moulding
One solution to this problem is to use only vacuum to drive long-range resin flow and enclose the laminate in a bag rather than in a matched pair of moulds. This technique is known by various names, and/or the respective abbreviations/acronyms [37-44] including resin infusion under flexible tooling (RIFT), the Seeman Composites Resin Infusion Molding Process (SCRIMPTM) [45] and Vacuum-Assisted Resin Transfer Moulding (VARTM). The technique is normally conducted without positive pressure, so that resin flow speeds are limited by the one atmosphere maximum pressure differential from full (low integer values in mbar) vacuum. Summerscales and Searle [42] analysed the various options and produced a four-level taxonomy for the set of processes forming a continuum between RTM and VB:
- RIFT1: in-plane flow parallel to the layers of reinforcement
- RIFT2: through-plane flow from a flow medium or scored core
- RIFT3: resin film infusion (RFI)
- RIFT4: partially pre-impregnated materials (also known as “semi-preg”)
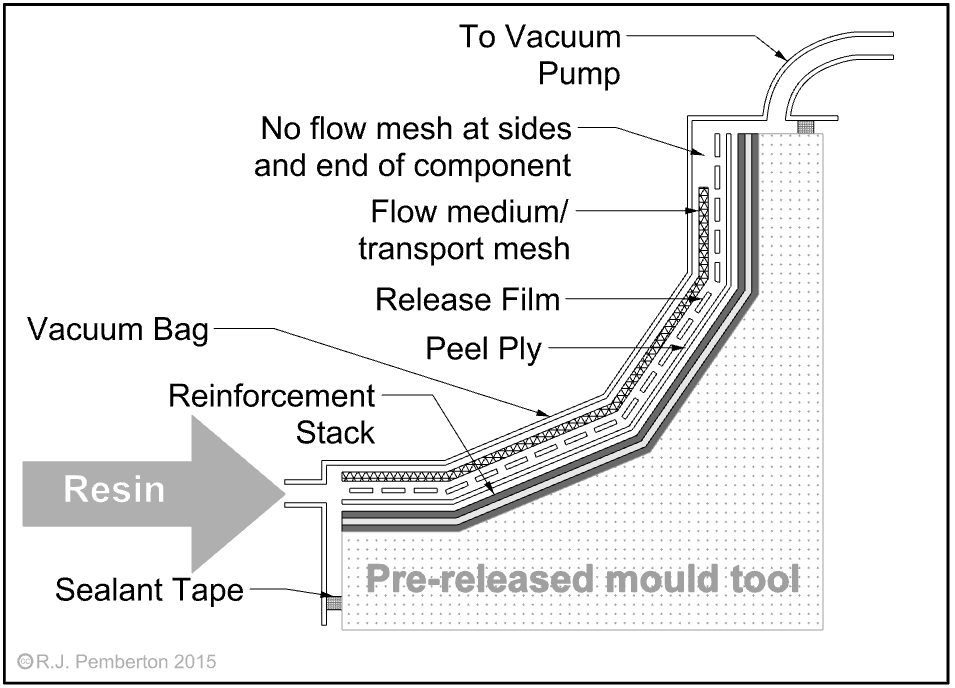
Figure 5*: Resin infusion under flexible tooling with a flow medium (RIFT II)
RFI uses un-reinforced B-staged resin film stacked with the dry reinforcement fabrics [46]. The process minimises the resin flow distance by utilising only through-thickness flow and uses the resin in a form where the base/hardener mix ratio is set by the materials supplier. Commercial versions of this process are Carboform (Cytec), HexFITTM (Hexcel Composites), SPRINTTM (SP Systems) and ZPREG (Umeco, formerly Advanced Composites Group).
5 Automated processes (filament winding, AFP/ATL and pultrusion)
Automated processes [47] include filament winding [48-50], robot-assisted placement [51] including Automatic Fibre Placement (AFP) [52] and Automated Tape Laying (ATL) and pultrusion/pulforming [53-56].
Filament winding is used for production where the components normally have an axis of symmetry (e.g. masts, pipes or tanks). The fibres are passed through a resin impregnation stage before being wound onto a rotating mould tool (mandrel) in a variety of orientations according to a pre-defined winding pattern. McLarty [57] analysed the feasibility of filament winding on a hull shaped mandrel in such a way as to cover the mandrel with fibres at a variety of angles to yield a structure conforming to the contours of the mandrel. The feasibility was verified by winding a 1/48 scale hull. It was concluded that 62 metre ship hulls could be produced. Chappelear et al [58] conducted further study toward the filament winding of a 46-metre glass reinforced plastics ship hull. They reviewed winding machine and mandrel concepts and developed a 1/5 scale mandrel for the proposed mine sweeper-hunter (MSH) for the United States Navy.
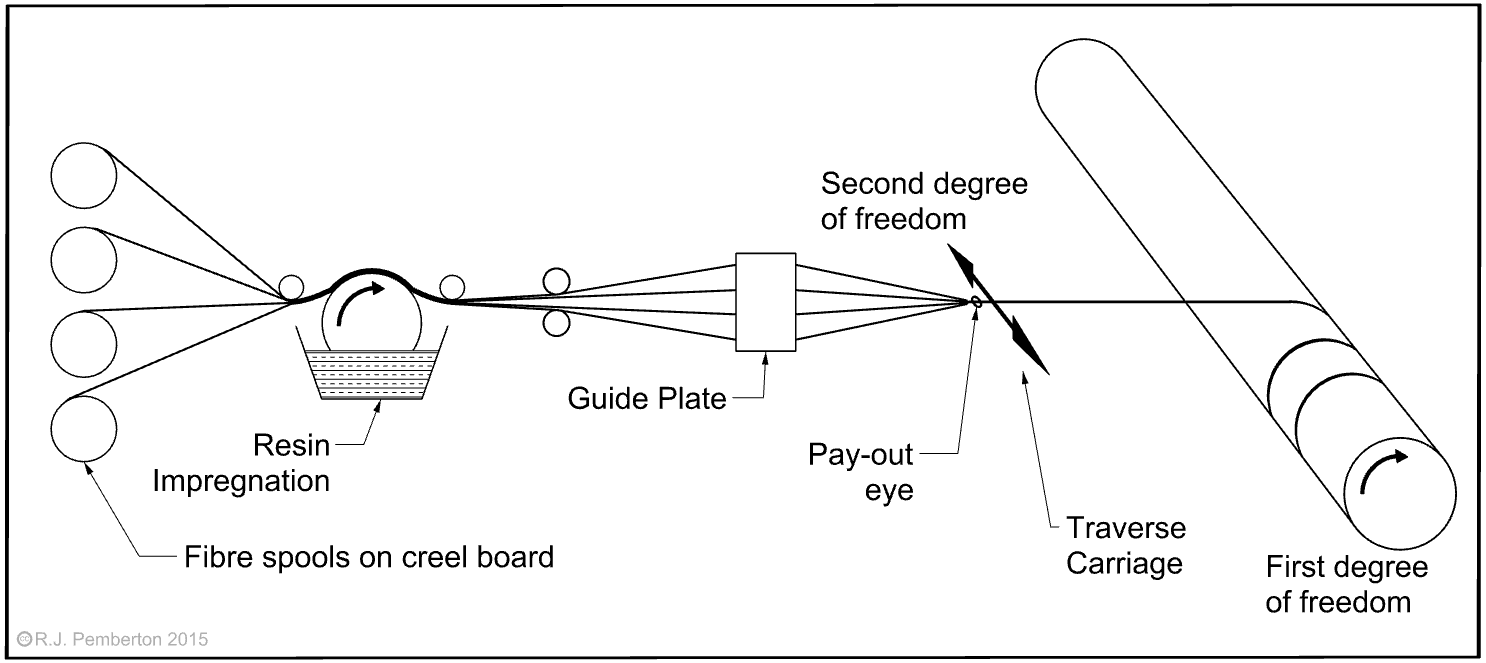
Figure 6*: Filament winding of a mast section
Pultrusion is similar to extrusion in that the component is normally a constant cross-section profile. In extrusion, the fibres would be broken into short lengths by the action of the extruder screw. In pultrusion, continuous fibres are pulled through a resin impregnation stage, marshalled into the profile cross-section and passed through a heated die from which they emerge as the solid profile. Pulforming is more appropriate for thermoplastics, or partially cured thermosets, and involves deliberate distortion of the pultruded section before final solidification.
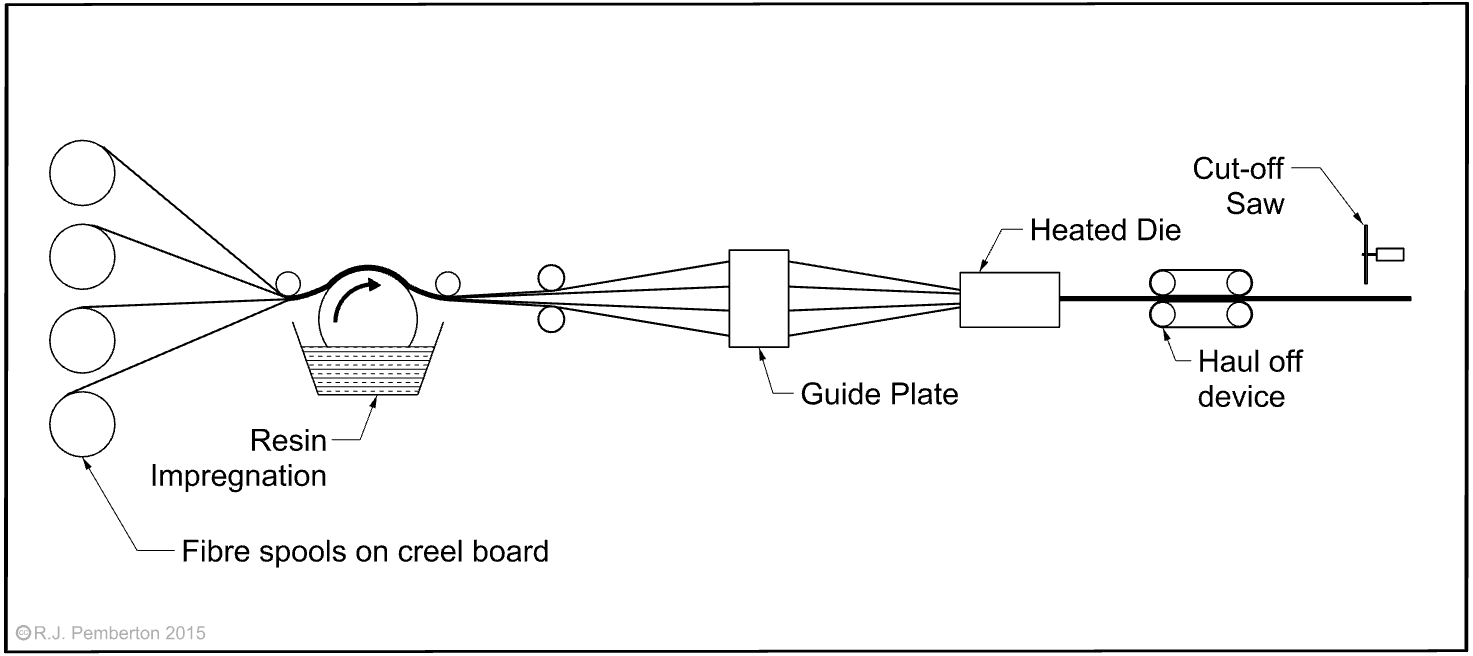
Figure 7*: Pultrusion
6 Miscellaneous techniques (tube rolling, machining, bonding and repair)
Tube rolling (mandrel wrapping) is a technique where prepreg blanks are formed onto a mandrel and consolidated normally using shrink-wrap.
Machining of composites has been reviewed by various authors [59-65]. Adhesive bonding for composites has been reviewed by Baldan [66, 67], Banea and da Silva [68] and Parashar and Mertiny [69]. Methodologies for the care and repair of composites have been presented by Armstrong et al [70].
7 Thermoplastic matrix composites
Thermoplastics are normally processed by increasing the temperature of the polymer to reduce the viscosity, moulding to shape, and cooling while holding the shape to produce a solid. Strictly, only crystalline polymers melt as amorphous, or the amorphous part of partially crystalline, polymers are essentially a morphology with liquid characteristics but insufficient energy to act as regular liquids. The effect of processing conditions on polymer properties has been discussed by Michaeli and Koschmieder [71].
For the bulk manufacture of short-fibre reinforced thermoplastics, the most successful processes are extrusion [72], and injection moulding [73-75]. In both processes, the fibres are broken down to short lengths during processing, so these technologies are not relevant to advanced (i.e. high-performance continuous fibre reinforced polymer matrix) composites.
Continuous fibre thermoplastic matrix composites can be manufactured by vacuum bagging (although high-temperature resistant bagging films are expensive and autoclave pressures are generally higher), compression moulding [76], liquid moulding [77], sheet forming [78] and the various automated processes [79-81].
The liquid composite moulding (RTM and RIFT) process are also possible if the monomer is injected and polymerised at the same time as the infusion of the reinforcement, usually at elevated temperatures [82]. The most common systems are ring-opening monomers to produce either polyamides (e.g. PA6 from caprolactam or PA12 from laurolactam) or polyesters (PBT from cyclic butylene terephthalate).
When a thermoplastic matrix is used, the equivalent of the RFI process is known as film-stacking.
Halmatic co-ordinated an EU FP4 BRITE-EurAm project (Enviro(n)Comp BE-3152/BRPR-CT96-0228)to research, develop and evaluate the use of environmentally friendly advanced thermoplastic composites for the manufacture of large surface area structures, specifically a glass fibre-reinforced polypropylene boat. Otheguy [83] states that the project used air-textured co-mingled glass and polypropylene fibre strands (now marketed as Twintex®) for the manufacture of the technology demonstrator: the first thermoplastic composite rigid inflatable boat (RIB). BAE
Systems, the industrial partner in the project, used the technology to manufacture "very cost-effective, simple-shaped assault boats" and other experimental RIBs including a Twintex® Atlantic 85 tested in service by the
Royal National Lifeboat Institution (RNLI). there may be additional information in Papin's thesis [84]. The project, was awarded the JEC Composite Award 2000 for transport innovation [85, 86].
Co-mingled glass/polypropylene was used by ÉireComposites to manufacture the 4.6 m 2win Twincat monocoque catamaran launched commercially in 2005 [87] and by the German boat builder Mega Sports Vertriebs for a set of 3 m open canoes in 2008 [88].
8 Aligned discontinuous fibre composites
Such et al [89] present an overview of the history of aligned discontinuous fibre composites. They focus on the process and application of highly aligned advanced composites with properties that approach those of continuous fibre composites. Aligned discontinuous fibre composites may be created by aligning short fibres or introducing discontinuities into aligned fibres in order to produce components with complex topologies.
9 Natural fibre reinforced composites
Faruk and Bledzki [90] and Summerscales and Grove [91] have reviewed the manufacturing methods that may permit the conversion of natural fibres into industrial composites. The key constraints are the hydrophilic nature of the fibres (and hence moisture release in process) and the temperature sensitivity of the fibres limits the time at temperature during processing. A moisture removal stage is considered an essential part of the manufacturing cycle. The processes that are most commonly used for engineered natural fibre composites are compression moulding for both thermoplastics and thermosets and resin transfer moulding or resin infusion for thermosets.
10 Process modelling and monitoring
Process modelling has been reviewed by Advani and Sozer [92] and Lynam and Milani [93]. Process monitoring techniques have been reviewed by Summerscales [94].
11 End-of-Life composites
A number of authors [95-102] have reviewed the recycling technologies appropriate to advanced composites. A broader consideration of the disposal of production waste and end-of-life composites has been presented by Summerscales et al [103].
* Acknowledgement
I offer sincere thanks to Richard Pemberton for drawing the Figures.
References
- BT Åström, Manufacturing of Polymer Composites, Chapman and Hall, London, 1997. ISBN 0-412-81960-0.
- TG Gutowski, Advanced Composites Manufacturing, John Wiley, New York, 1997. ISBN 0-471-15301-x.
- RS Davé and AC Loos, Processing of Composites, Hanser Publishers, Munich, 1999. ISBN 1-56990-226-7.
- G Akovali, Handbook of Composite Fabrication, RAPRA Technology Limited, Shawbury, 2000. ISBN 1-85957-263-4. Woodhead Publishing, Cambridge, 2001. ISBN-13: 978-1-85957-263-4.
- L Boogh and R Mezzenga, Processing principles for thermoset composites, Chapter 2.19 in R Talreja and J-A Månson (editors) Volume 2: Polymer Matrix Composites (Comprehensive Composite Materials), Elsevier Science, 2000, 671-699. ISBN 0-08-043720-6.
- J-AE Månson, MD Wakeman and N Bernet, Composite processing and manufacturing: an overview, Chapter 2.16 in Talreja, R and Månson J-AE (editors): Volume 2: Polymer Matrix Composites (Comprehensive Composite Materials), Elsevier Science, 2000, 577-607. ISBN 0-08-043720-6.
- SK Mazumdar, Composites Manufacturing: materials, product and process engineering, CRC Press, Boca Raton FL, 2002. ISBN 0-8493-0585-3.
- F Campbell, Manufacturing Processes For Advanced Composites, Elsevier, December 2003. ISBN 978-1-85617-415-2.
- AB Strong, Fundamentals of Composites Manufacturing: materials, methods and applications, Society of Manufacturing Engineers, Dearborn, 2008. ISBN_978-0-87263-854-9.
- SV Hoa, Principles of the Manufacturing of Composite Materials, DEStech Publications, 2009. ISBN 978-1-932078-26-8.
- S Advani and K-T Hsiao (editors), Manufacturing techniques for polymer matrix composites (PMCs), Woodhead Publishing, Cambridge, 2012. ISBN 978-0-85079-067-6. ISBN 978-0-85079-625-8 (ebook).
- S Grove, Manufacture of Polymer Composites, In L Nicolais and A Borzacchiello (editors), Wiley Encyclopedia of Composites, John Wiley & Sons, Hoboken NJ, 2012, 1506-1525. ISBN print: 978-0-470-12828-2.
12a: S Syngellakis (editor), Composites: advances in manufacture and characterisation, WIT Press, Southampton, 2016. ISBN 978-1-78466-167-0.
12b: PK Mallick, Processing of Polymer Matrix Composites, CRC Press, Boca Raton FL, 2017. ISBN 978-1-4665-7822-7.
12c: K Debnath and I Singh, Primary and Secondary Manufacturing of Polymer Matrix Composites, CRC Press, Boca Raton FL, 2017. ISBN 978-1-4987-9930-0.
- V Shukla, M Bajpai, DK Singh, M Singh and R Shukla, Review of basic chemistry of UV: curing technology, Pigment and Resin Technology, 2004, 33(5), 272 – 279.
- W Rogers, C Hoppins, Z Gombos and J Summerscales, In-mould gel-coating of polymer composites: a review, Journal of Cleaner Production, 2014, 70, 282-291.
- C Di Tomasso, ZJ Gombos and J Summerscales, Styrene emissions during gel-coating of composites, Journal of Cleaner Production, 83, 317-328.
- J Guilon, Production and design aspects of craft over 90 ft (27 m) in length, Symposium on Reinforced Plastics: recent advances in the marine field, Plastics and Rubber Institute, Southampton, 27 September 1972, Paper 6.
- CS Smith, Applications of fibre reinforced composites in marine technology, Proceedings of the Conference on Composites - Standards, Testing and Design, National Physical Laboratory, Teddington, 8-9 April 1974, 54-69.
- PR Ciriscioli and GS Springer, Smart autoclave cure of composites, Technomic Publishing, Lancaster PA, 1990. ISBN_0-87762-802-5.
- JC Seferis, RW Hillermeier and FU Buehler, Prepregging and autoclaving, Chapter 20 in R Talreja and J-A Månson (editors): Comprehensive Composite Materials Encyclopædia, volume 2: Polymer Matrix Composites, Elsevier, Oxford, 2000, pages 701-736.
- K Noakes, Successful composite techniques: a practical introduction to the use of modern composite materials, fourth edition, The Crowood Press, Marlborough UK, August 2008. ISBN-13: 978-1-84797-054-1.
- S McBeath and B O'Rourke, Competition car composites: a practical handbook - second edition, Haynes, Sparkford UK, 2009. ISBN-13: 978-1-84425-701-0.
- RS Davé, M Henne, B Louis and P Ermanni, Processing: autoclave modeling, In L Nicolais and A Borzacchiello (editors), Wiley Encyclopedia of Composites, John Wiley & Sons, Hoboken NJ, 2012, 2443-2454.
- M Giordano, V Antonucci and A Langella, Processing: Autoclave, In L Nicolais and A Borzacchiello (editors), Wiley Encyclopedia of Composites, John Wiley & Sons, Hoboken NJ, 2012, 2437-2442. ISBN print: 978-0-470-12828-2.
- B Louis and P Ermanni, Out-of-Autoclave Prepreg Processing, In L Nicolais and A Borzacchiello (editors), , Wiley Encyclopedia of Composites, John Wiley & Sons, Hoboken NJ, 2012, 2052-2058. ISBN print: 978-0-470-12828-2.
- T Centea, LK Grunenfelder and SR Nutt, A review of out-of-autoclave prepregs – material properties, process phenomena, and manufacturing considerations, Composites Part A: Applied Science and Manufacturing, March 2015, 70, 132-154.
- M Revellino, L Saggese and E Gaiero, Compression Molding of SMCs, Chapter 2.22 in R Talreja and J-A Månson (editors): Comprehensive Composite Materials Encyclopædia, volume 2: Polymer Matrix Composites, Elsevier, Oxford, 2000, 763-805.
- AI Isayev, Molding: compression, In L Nicolais and A Borzacchiello (editors), Wiley Encyclopedia of Composites, John Wiley & Sons, Hoboken NJ, 2012, 1853-1869. ISBN print: 978-0-470-12828-2.
- K van Harten, Production by resin transfer moulding, in R A Shenoi and J F Wellicome (editors): Composite Materials in Maritime Structures, Cambridge University Press, Cambridge, 1993, Chapter 4, 86-126.
- K Potter, Resin Transfer Moulding, Chapman and Hall, London, 1997. ISBN_0-412-72570-3.
- CD Rudd, AC Long, KN Kendall and CGE Mangin, Liquid Moulding Technologies, Woodhead Publishing, Cambridge, 1997. ISBN 1-85573-242-4.
- SW Beckwith and CR Hyland, Resin Transfer Molding: a decade of technology advances, SAMPE Journal, November/December 1998, 34(6), 7-19.
- TM Kruckenberg and R Paton (editors), Resin Transfer Moulding for Aerospace Structures, Kluwer Academic Publishers, Dordrecht NL, 1998. ISBN 0-412-73150-9.
- WP Benjamin and SW Beckwith, Resin Transfer Moulding, SAMPE Monograph 3, Covina CA, 1999. ISBN 0-938-99483-2.
- RS Parnas, Liquid Composite Moulding, Hanser Gardner Publications, 2000. ISBN 1-569-90287-9.
- S Advani and EM Sozer, Liquid molding of thermoset composites, Chapter 23 in R Talreja and J-A Månson (editors): Comprehensive Composite Materials Encyclopædia, volume 2: Polymer Matrix Composites, Elsevier, Oxford, 2000, pages 807-844.
- P Ermanni, C Di Fratta and F Trochu, Molding: liquid composite molding (LCM), In L Nicolais and A Borzacchiello (editors), Wiley Encyclopedia of Composites, John Wiley & Sons, Hoboken NJ, 2012, 1884-1893. ISBN print: 978-0-470-12828-2.
- CD Williams, J Summerscales and SM Grove, Resin infusion under flexible tooling (RIFT): a review, Composites Part A: Applied Science and Manufacturing, July 1996, 27A(7), 517-524.
- D Abraham and R McIlhagger, A review of liquid injection techniques for the manufacture of aerospace composite structures, Polymers and Polymer Composites, 1996, 4(6), 437-444.
- FC Smith, The current status of resin infusion as an enabling technology for toughened aerospace structures, Materials Technology, 1999, 14(2), 71-80.
- D Cripps, TJ Searle and J Summerscales, Open Mould Techniques for Thermoset Composites, Chapter 21 in R Talreja and J-A Månson (editors): Comprehensive Composite Materials Encyclopædia, volume 2: Polymer Matrix Composites, Elsevier Science, Oxford, July 2000, pp 737-761. Set ISBN: 0-08-043720-6. Volume ISBN: 0-08-043725-7.
- A Cocquyt, Infusion revisited, Professional Boatbuilder, February/March 2001, (69), 132-149.
- J Summerscales and TJ Searle, Low pressure (vacuum infusion) techniques for moulding large composite structures, Proc IMechE Part L - Journal of Materials: Design and Applications, February 2005, L219(1), 45-58.
- SW Beckwith, Resin Infusion Technology * Part 1 - Industry highlights * Part 2 - Process definitions and industry variations * Part 3 - A detailed overview of RTM and VIP infusion processing, SAMPE Journal, 2007, 43(1), 61 and 43(3), 46 and 43(4), 6 & 66-70.
- J Summerscales, Resin Infusion Under Flexible Tooling (RIFT), In L Nicolais and A Borzacchiello (editors): Encyclopedia of Composites – second edition, John Wiley & Sons, 2012, 2648-2658. ISBN print: 978-0-470-12828-2.
- Anon., SCRIMP technology, http://www.tpicomposites.com/?id=9, accessed 13:25 on 10 May 2008.
- G Marsh, Resin film infusion – composites cost reducer, Reinforced Plastics, February 2002, 46(2), 44-49.
- A Yenilmez-Gurkok and IN Tanse, Manufacturing Automation, Polymer Composites, In L Nicolais and A Borzacchiello (editors), Wiley Encyclopedia of Composites, John Wiley & Sons, Hoboken NJ, 2012, 1526-1534. ISBN print: 978-0-470-12828-2.
- M Munro, A review of manufacturing of fiber composite components by filament winding, Polymer Composites, October 1988, 9(5), 352-359.
- ST Peters, WD Humphrey and RF Foral, Filament winding composite structure fabrication, SAMPE, Covina CA, 1991. ISBN 0-938994-55-7. Second edition, 1999. ISBN_0-938994-81-6.
- S Koussios and A Beukers, Filament Winding: Design, Materials, Structures and Manufacturing Processes, In L Nicolais and A Borzacchiello (editors), Wiley Encyclopedia of Composites, John Wiley & Sons, Hoboken NJ, 2012, 1011-1026. ISBN print: 978-0-470-12828-2.
- GC Newell, RO Buckingham and K Khodabandehloo, The automated manufacture of prepreg broadgoods components - a review of literature, Composites Part A: Applied Science and Manufacturing, 1996, 27(3), 211-217.
- A Crosky, C Grant and D Kelly, Fiber Placements, In L Nicolais and A Borzacchiello (editors), Wiley Encyclopedia of Composites, John Wiley & Sons, Hoboken NJ, 2012, 945-949. ISBN print: 978-0-470-12828-2.
- RW Meyer, Handbook of pultrusion technology, Chapman and Hall, London, 1985. ISBN 0-412-00761-4.
- TF Starr, Pultrusion for engineers, Woodhead, Cambridge, 2000. ISBN_1-85573-425-7.
- WB Goldsworthy, Pulforming, In L Nicolais and A Borzacchiello (editors), Wiley Encyclopedia of Composites, John Wiley & Sons, Hoboken NJ, 2012, 2542-2544. ISBN print: 978-0-470-12828-2.
- A Vázquez and M Escobar, Pultrusion, In Nicolais, L. and Borzacchiello ,Wiley Encyclopedia of Composites, John Wiley & Sons, Hoboken NJ, 2012, 2545-2560. ISBN print: 978-0-470-12828-2.
- JL McLarty, Feasibility of filament winding large ship hulls, McClean-Anderson report J2016, December 1981. AD A125 771: http://www.dtic.mil/cgi-bin/GetTRDoc?Location=U2&doc=GetTRDoc.pdf&AD=ADA125771, accessed 10 March 2015.
- DN Chappelear, T Aochi and RJ Milligan, Filament winding of a ship hull, Lockheed report LMSC-D945 402, October 1983. AD A134 577: http://www.dtic.mil/cgi-bin/GetTRDoc?Location=U2&doc=GetTRDoc.pdf&AD=ADA134577, accessed 10 March 2015.
- S Abrate and DA Walton, Machining of composite materials. Part 1: traditional methods, Composites Manufacturing, 1992, 3(2), 75-83.
- S Abrate and D Walton, Machining of composite materials. Part 2: non-traditional methods, Composites Manufacturing, 1992, 3(2), 85-94.
- S Gordon and MT Hillery, A review of the machining of composite materials, Proc IMechE Part L: Journal of Materials Design and Applications, 2003, L217(1), 35-45.
- GM Robinson, MJ Jackson and MD Whitfield, A review of machining theory and tool wear with a view to developing micro and nano machining processes, Journal of Materials Science, March 2007, 42(6), 2002-2015.
- VS Sharma, M Dogra and NM Suri, Advances in the turning process for productivity improvement - a review, Proceedings of the Institution of Mechanical Engineers, Part B: Journal of Engineering Manufacture, 2008, 222(11), 1417-1442.
- AB Sadat, Machining of Composites, In L Nicolais and A Borzacchiello (editors), Wiley Encyclopedia of Composites, John Wiley & Sons, Hoboken NJ, 2012, 1497-1505. ISBN print: 978-0-470-12828-2.
- JY Sheikh-Ahmad and JP Davim, Cutting and machining of polymer composites, In L Nicolais and A Borzacchiello (editors),Wiley Encyclopedia of Composites, John Wiley & Sons, Hoboken NJ, 2012, 648-657. ISBN print: 978-0-470-12828-2.
- A Baldan, Adhesively-bonded joints and repairs in metallic alloys, polymers and composite, Journal of Materials Science, January 2004, 39(1), 1-49.
- A Baldan, Adhesively-bonded joints in metallic alloys, polymers and composite materials: mechanical and environmental durability performance, Journal of Materials Science, August 2004, 39(15), 4729-4797.
- MD Banea and LFM da Silva, Adhesively bonded joints in composite materials: an overview, Proceedings of the Institution of Mechanical Engineers, Part L: Journal of Materials: Design and Applications, 2009, 223(1), 1-18.
- A Parashar and P Mertiny, Adhesively bonded composite tubular joints: review, International Journal of Adhesion and Adhesives, October 2012, 38, 58-68.
- KB Armstrong, G Bevan and WF Cole, Care and Repair of Advanced Composites - second edition, SAE International, Warrendale PA, 2005. ISBN 0-7680-1062-4.
- W Michaeli and M Koschmieder, Processing principles for thermoplastic polymers, Chapter 25 in R Talreja and J-A Månson (editors): Comprehensive Composite Materials Encyclopædia, volume 2: Polymer Matrix Composites, Elsevier, Oxford, 2000, 853-872.
- L Incarnato and L di Maio, Polymeric extrusion, In L Nicolais and A Borzacchiello (editors), Wiley Encyclopedia of Composites, John Wiley & Sons, Hoboken NJ, 2012, 2225-2243. ISBN print: 978-0-470-12828-2.
- R Brooks, Injection molding based techniques, Chapter 2.30 in R Talreja and J-A Månson (editors) Volume 2: Polymer Matrix Composites (Comprehensive Composite Materials), Elsevier Science, 2000. pp 999-1028. ISBN 0-08-043720-6.
- SG Advani, Molding: short-fiber composites ~ flow processing, In L Nicolais and A Borzacchiello (editors), Wiley Encyclopedia of Composites, John Wiley & Sons, Hoboken NJ, 2012, 1894-1906. ISBN print: 978-0-470-12828-2.
- F Ehrig, Molding: polymer injection, In L Nicolais and A Borzacchiello (editors), Wiley Encyclopedia of Composites, John Wiley & Sons, Hoboken NJ, 2012, 1870-1883. ISBN print: 978-0-470-12828-2.
- MD Wakeman and CD Rudd, Compression molding of thermoplastic composites, Chapter 2.27 in R Talreja and J-A Månson (editors): Comprehensive Composite Materials Encyclopædia, volume 2: Polymer Matrix Composites, Elsevier, Oxford, 2000, 915-963.
- P-E Bourban, Liquid molding of thermoplastic composites, Chapter 2.28 in R Talreja and J-A Månson (editors) Volume 2: Polymer Matrix Composites (Comprehensive Composite Materials), Elsevier Science, 2000, 965-977.
- PJ Mallon and CM Óbrádaigh, Compliant mold techniques for thermoplastic composites, Chapter 2.26 in R Talreja and J-A Månson (editors): Volume 2: Polymer Matrix Composites (Comprehensive Composite Materials), Elsevier Science, 2000, 873-913.
- AG Gibson, Continuous molding of thermoplastic composites, Chapter 2.29 in R Talreja and J-A Månson (editors) Volume 2: Polymer Matrix Composites (Comprehensive Composite Materials), Elsevier Science, 2000, 979-998.
- C Sohl, Continuous molding of thermoset composites, Chapter 2.24 in R Talreja and J-A Månson (editors): Comprehensive Composite Materials Encyclopædia, volume 2: Polymer Matrix Composites, Elsevier, Oxford, 2000, 845-852.
- P Mitschang, Manufacturing of thermoplastic fiber-reinforced polymer composites, In L Nicolais and A Borzacchiello (editors), Wiley Encyclopedia of Composites, John Wiley & Sons, Hoboken NJ, 2012, 1548-1562. ISBN print: 978-0-470-12828-2.
- K van Rijswijk and HEN Bersee, Reactive processing of textile fiber-reinforced thermoplastic composites: an overview, Composites Part A: Applied Science and Manufacturing, March 2007, 38(3), 666–681.
- ME Otheguy, Manufacture, repair and recycling of thermoplastic composite boats, PhD, Newcaste University, July 2010.
- P Papin, Etude et choix de matériaux polymères ou composites pour la réalisation d'une forme creuse - projet canoë biplace pour la randonnée (Study and selection of polymeric materials or composites for the creation of a hollow shape – two-seater canoe for excursions), Thèse de doctorat en Sciences des matériaux (sous la direction de Yves Bertin), Université de Poitiers (TS 97/POIT/2299), 1997. Hover over thesis title to see the abstract.
- Twintex and 2win's new twincat, European Boatbuilder, March 2006. (18), 4.
- Twintex® technical fabric from Owens Corning chosen for innovative vacuum bag molded thermoplastic composite canoe, Owens Corning news release, 2008, accessed 15 February 2015.
- G Boyce and F Gouardères, New composite sets sail, RTD info, September 2000, (27), 15.
- Anon., Brite-Euram project awarded top composites prize, 2000. http://cordis.europa.eu/news/rcn/15012_en.html, accessed 12 March 2015.
- M Such, C Ward and K Potter, Aligned discontinuous fibre composites: a short history, Journal of Multifunctional Composites, 2014, 2(3)
- O Faruk and AK Bledzki, Processing of Biofiber-Reinforced Composites, In L Nicolais and A Borzacchiello (editors), Wiley Encyclopedia of Composites, John Wiley & Sons, Hoboken NJ, 2012, 2465-2479. ISBN print: 978-0-470-12828-2.
- J Summerscales and S Grove, Manufacturing Methods for Natural Fibre Composites, Chapter 7 in A Hodzic and R Shanks (editors): Natural Fibre Composites: materials, processes and properties, Woodhead Publishing, Cambridge, 2014, 176-215. ISBN 978-0-85709-524-4 (print). ISBN 978-0-85709-922-8 (online).
- SG Advani and ME Sozer, Process Modeling in Composites Manufacturing, Taylor and Francis, London, 2002. ISBN_0-82470-860-1. Second edition, CRC Press, July 2010. ISBN 978-1-42009082-6.
- C Lynam and AS Milani, A Guide to Modeling Thermoplastic Composite Manufacturing Processes: optimizing process variables and tooling design using finite element analysis, DEStech Publications, Lancaster PA, September 2014. ISBN 978-1-60595-042-6.
- J Summerscales, Chapter 2: In-process monitoring for control of closed-mould techniques for the manufacture of thermosetting matrix composites, pages 57-101 in GO Shonaike and SG Advani (editors): Advanced Polymeric Materials - Structure Property Relationships, CRC Press LLC, Boca Raton FL, 2003. ISBN 1-58716-047-1.
- JM Henshaw, W Han and AD Owens, An overview of recycling issues for composite materials, Journal of Thermoplastic Composite Materials, 1996, 9(1), 4-20.
- SJ Pickering, Recycling technologies for thermoset composite materials: current status, Composites Part A: Applied Science and Manufacturing, August 2006, 37(8), 1206-1215.
- S Pimenta and ST Pinho, Recycling carbon fibre reinforced polymers for structural applications: technology review and market outlook, Waste Management, February 2011, 31(2), 378–392.
- L Scelsi, A Hodzic, C Soutis, SA Hayes, S Rajendran, MA AlMa’adeed and R Kahraman, A review on composite materials based on recycled thermoplastics and glass fibres, Plastics, Rubber and Composites, 2011, 40(1), 1-10.
- G Oliveux, J-L Bailleul and ELG La Salle, Chemical recycling of glass fibre reinforced composites using subcritical water, Composites Part A: Applied Science and Manufacturing, November 2012, 43(11), 1809-1818.
- Y Yang, R Boom, B Irion, D-J van Heerden, P Kuiper and H de Wit, Recycling of composite materials, Chemical Engineering and Processing: Process Intensification, 2012, 51, 53–68.
- E Asmatulu, J Twomey and M Overcash, Recycling of fiber-reinforced composites and direct structural composite recycling concept, Journal of Composite Materials, 2014, 48(5), 593–608.
- G Oliveux, LO Dandy and GA Leeke, Current status of recycling of fibre reinforced polymers: review of technologies, reuse and resulting properties, Progress in Materials Science, July 2015, 72, 61-99.
- J Summerscales, MM Singh and K Wittamore, Disposal of composite boats and other marine composites, Chapter 8 in J Graham-Jones and J Summerscales (editors): Marine Applications of Advanced Fibre-Reinforced Composites, Elsevier/Woodhead, Cambridge, 2015. ISBN 978-1-78242-250-1.
Created by John Summerscales on 22 July 2010, converted to HTML on 12 October 2011, Figures added on 24-May-2015 and updated on
06-Oct-2023 16:51. Terms and conditions. Errors and omissions. Corrections.