Composites Design and Manufacture (Plymouth University teaching support materials)
Interfaces. Interphases. Meso-mechanics (fibre clustering and resin-rich volumes). Voids. |
Lecture PowerPoint |
Review papers |
Subject Index |
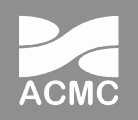 |
Interfaces
An interface is the distinct region where the reinforcement (fibre) and the matrix (polymer) meet. The topic of interfaces has been reviewed by several authors [1-7]. For more on coupling agents, used to promote good fibre-to-matrix bonding, see coupling agents on the Fibres page.
Interphases
An interphase is formed when there is a reaction between the reinforcement and the matrix [8, 9]. For example, titanium carbide may be formed when carbon fibres are used in a titanium matrix. Jancar [10] has reviewed the role of the interphase in the control of composite performance.
Meso-mechanics (including clustering of reinforcement and consequent resin-rich volumes)
Mesomechanics [11] is the area that bridges the microstructure-property relationship of materials with non-continuum mechanics. It is aimed at developing the fundamental principles and the associated methodologies which can guide the creation of multiphase materials with desired microstructures balanced by prediction of their in-service microscopic and macroscopic behaviours. The US Air Force Office of Scientific Research (AFOSR) research initiative encompassed fundamental studies in the following general areas:
- constitutive modelling of multiphase materials
- damage mechanics of multiphase materials
- stress waves and dynamic responses
- very high temperature behaviour
- non-linear structural behaviour
- computational and experimental mechanics.
The nature of fibre-reinforced composites is such that there is generally dual-scale structure with clustering of fibres in bundles (tows) and larger features dictated by the reinforcement architecture (e.g. chopped strand mat, woven fabrics or stitched non-crimp fabrics (NCF)). This data required for rules-of-mixture may be insufficient for a full description of the meso-structures where clustering of fibres occurs. The use of image processing and analysis for the characterisation of composite micro-/meso-structures has been the subject of a number of publications (e.g. Guild and Summerscales [12]. Pyrz [13, 14]. Summerscales [15]. Summerscales et al [16]. The structures within clustered populations have been described using a variety of parameters, e.g.
- nearest-neighbour index [17],
- chi-squared analysis [18],
- quadrat analysis [19],
- mean free path and mean random spacing [20],
- space auto-correlograms [21],
- area fraction variance analysis and mean intercept length [22],
- contiguity index for hybrids [23],
- and in recent years, tessellation techniques (e.g. Delauney [24] or Voronoi [16], or
- fractal dimensions [24]
Mulligan et al [25] reviewed the experimental and theoretical work relevant to the effects of fibre-bundling on the mechanical properties of a short-fibre composite. They identified a variety of techniques that have been used to control fibre-bundling in composite materials, but that none of those techniques were entirely satisfactory to study the effect of fibre-bundling on the mechanical properties. Davy and Guild [26] have studied the distribution of inter-particle distances. Summerscales et al [16] have used Voronoi tessellation and fractal dimension to correlate mechanical properties and processability to the microstructure of fabric-reinforced polymer matrix composites.
In the context of natural fibre composites, Baley et al [27] stated that "Fiber clusters and bundles promote damage initiation and fracture propagation; to improve composite quality and performance, it is necessary to improve the separation and dispersion of fibers by optimising both the extraction procedures and manufacturing conditions"
Varghese and Whitcomb [28] have used a local averaging procedure to determine effective properties for a reinforcement that has microstructure, specifically using finite element analysis to study the effect of homogenisation for the modelling of hollow fibres. The homogenised properties can potentially be used to eliminate one level of microstructure when modelling such systems.
Virtual testing is an emerging framework for integrated modelling of multiple lengthscales (Table 1), typically from atom to macroscale.
Table 1: Indicative lengthscales typically used in virtual testing frameworks
atom |
nanoscale |
microscale |
mesoscale |
macroscale |
structural |
10-10m
Å: Ångström |
10-9m
nm: nanometre |
10-8m |
10-7m |
10-6m
μm: micrometre |
10-5m |
10-4m |
10-3m
mm: millimetre |
10-2m
cm: centimetre |
10-1m |
100m
m: metre |
101m |
102m |
Voids
The process by which composites are manufactured can entrap air (or volatiles) in the laminate as porosity or voids. The causes may include (i) air in the resin mix, (ii) volatiles in the resin "boiling", (iii) the degree of impregnation of pre-impregnated materials, (iv) trapping air between prepreg layers, or (v) race-tracking in liquid composite moulding processes. Thorfinnson and Biermann [29] proposed that the degree of impregnation (DI) could be calculated using the interstitial volume (IV: the space between the dry fibres) and the pore volume (PV) of the prepreg using DI = (IV-PV)/IV.
Judd and Wright [30], Ghiorse [31], Baley et al [32], Liu and Chen [33] and Mehdikhani et al [34] have reviewed porosity/voids in composites. Judd and Wright concluded that "although there is a considerable scatter in results (reflecting in part the difficulties of accurate void content determination) the available data show that the interlaminar shear strength of composites decreases by about 7 per cent for each 1 per cent voids up to at least the 4 per cent void content level, beyond which the rate of decrease diminishes. Other mechanical properties may be affected to a similar extent. This is true for all composites regardless of the resin, fibre or fibre surface treatment used in
their fabrication". See Table 1 of the reference for a comprehensive analysis of the data.
Purslow [35] proposed a novel classification system for voids. He suggested that the current system is only significant for fairly uniformly distributed voids. For example, to quote a Vv (void volume fraction) of 0.5% for a composite of generally high quality (voids < 0.2%) but with an occasional very large void could be very misleading and potentially dangerous. It is difficult to measure void contents to such low values. He suggested that the void content should be quoted as "0<voids<0.2%; infrequent local voids > 0.5%". His studies have suggested that when Vv < 0.5%, the voids are spherical with a diameter of 10 μm and are due to trapped volatiles. As Vv increases, the voids due to trapped volatiles decrease in number and are replaced by large intra-tow/intra-lamina voids. The results suggested a linear relationship between Vv and void thickness, where the thickness is related to fibre diameter.
Stone and Clarke [36] reported that below Vv = 1.5% voids tend to be volatile-induced and hence spherical with diameters in the range 5-20 μm, while above Vv = 1.5% the voids are flattened and elongated in the in-plane direction due to the limitation of space between the fibre bundles and are also significantly larger than those voids at a lower Vv. Mayr et al [37] have recently reported that small pores in CFRP with porosity levels <1.8% often have roughly circular cross-sections and found an abrupt increase in the out-of-plane shape factors at this
percentage porosity.
Little et al [38] have presented a good summary of the options for the characterisation of voids in composites. The techniques available and their respective issues are shown in Table 2:
Table 2: Techniques for the characterisation of voids
|
Archimedes density |
Matrix burn-off |
Chemical digestion |
Water Absorption at 100°C |
Ultrasonic scanning |
Ultrasonic & DWT [39] |
Microscopy |
X-ray CT |
Data requirements |
fibre and matrix densities |
fibre and matrix densities |
fibre and matrix densities |
Limited use [40] |
calibration samples |
|
|
|
Can report negative void content |
✗ |
|
|
|
|
|
|
|
Can lose some fibre |
✗ |
✗ |
✗ |
|
|
|
|
|
Chemical hazard |
|
|
✗ |
|
|
|
|
|
Preparation time and costs |
|
|
|
|
|
|
✗ |
|
Sampling bias |
|
|
|
|
|
|
✗ |
|
2D shape and size information |
|
|
|
|
|
|
✓ |
✓ |
3D shape and size information |
|
|
|
|
|
|
|
✓ |
Applicable standards/guidance |
ASTM D3171 |
|
|
ISO 62:2008 |
CRAG test method 1001 |
|
CMH-17 §6.6.6.5.4 |
|
Madsen et al [41] considered that the porosity in plant (and other hollow) fibre composites can be divided into three components:
- fibre-correlated porosity, including (a) fibre porosity (the lumen), (b) fibre/matrix interface porosity and (c) impregnation porosity (where the reinforcement architecture denies the matrix resin access to inter-fibre spaces),
- matrix correlated porosity (bubbles in the resin), and
- structural porosity (where insufficient matrix is available to fill the free space in a fully compacted fibre assembly.
Madsen et al [41] suggest there is a transition value of fibre weight fraction which gives an optimal combination of high fibre volume fraction, high composite density and low porosity. They studied natural fibres (flax, hemp and
jute) in polymer matrix (polypropylene or polyethyleneterephthalate) composites and observed that the thermoplastic matrix is not able to impregnate the fibre lumen.
The webpage on Resin Transfer Moulding includes a section on void formation and transport.
References
- AC Metcalfe, Interfaces in Metal Matrix Composites (LJ Broutman and RH Crock - editors, Composite Materials series volume 1), Academic Press, New York and London, 1974. ISBN 0-12-136501-8. PU CSH Library
- EP Plueddemann, Interfaces in Polymer Matrix Composites (LJ Broutman and RH Crock - editors, Composite Materials series volume 6), Academic Press, New York and London, 1974. ISBN 0-12-136506-9.
- DL Caldwell, Interfacial analysis, In SM Lee - editor, Encyclopedia of Composites, VCH Publishers, New York, 1990, volume 2, 361-377. ISBN 0-89573-732-9. PU CSH Library.
- JDH Hughes, The carbon fibre/epoxy interface: a review, Composites Science and Technology, 1991, 41(1), 13-45.
- Jang-Kyo Kim and Yiu-wing Mai, High strength, high fracture toughness fibre composites with interface control: a review, Composites Science and Technology, 1991, 41(4), 333-378.
- MC Andrews, DJ Bannister and RJ Young, The interfacial properties of aramid epoxy model composites, Journal of Materials Science, 1 August 1996, 31(15), 3893-3913.
- LT Drzal, PJ Herrera-Franco and Henjen Ho. Fibre-Matrix Interface Tests, Chapter 5 in A Kelly and C Zweben - editors, Comprehensive Composite Materials volume 5, Pergamon, Oxford, 2000, 71-111. ISBN 0-08-043723-0.
- WD Bascom, Interphase in fiber-reinforced composites, In SM Lee - editor, Encyclopedia of Composites, VCH Publishers, New York, 1990, volume 2, 411-422. ISBN 0-89573-732-9. PU CSH Library.
- ST Mileiko, Interphases, Chapter 4.09.2.3 in A Kelly and C Zweben - editors, Comprehensive Composite Materials volume 4, Pergamon, Oxford, 2000, 268-270. ISBN 0-08-042993-9.
- J Jancar, Review of the role of the interphase in the control of composite performance on micro- and nano-length scales, Journal of Materials Science, October 2008, 43(20), 6747-6757.
- GK Haritos, JW Hager, AK Amos, MJ Salkind and ASD Wang, Mesomechanics: the microstructure-mechanics connection, International Journal of Solids and
Structures, 1988, 24(11), 1081-1096.
- F J Guild and J Summerscales, Microstructural image analysis applied to fibre composite materials: a review, Composites, 1993, 24(5), 383-394.
- R Pyrz, Chapter 1.16: Morphological characterization of microstructures, in Comprehensive Composite Materials, Volume 1: Fiber Reinforcements and General Theory of Composites, Elsevier, 2000, pp 465-478.
- R Pyrz, Chapter 2.15: The application of morphological methods to composite materials, in Comprehensive Composite Materials, Volume 2: Polymer Matrix Composites, Elsevier, 2000, pp 553-576.
- J Summerscales (editor), Microstructural Characterisation of Fibre-Reinforced Composites, Woodhead Publishing, Cambridge, July 1998. ISBN 1-85573-240-8.
- J Summerscales, N R L Pearce, P Russell and F J Guild, Voronoi cells, fractal dimensions and fibre composites, Journal of Microscopy, February 2001, 201(2), 153-162.
- P J Clark and F C Evans, Distance to the nearest neighbor as a measure of spatial relationships in populations, Ecology, October 1954, 35(4), 445-453. JSTOR.
- P Davis, Describing point patterns, in Science in Geography Book 3: Data Description and Presentation, Oxford University Press, Oxford, 1974, 29-35. ISBN 978-0-19-913067-2.
- P Greig-Smith, The use of random and contiguous quadrats in the study of the structure of plant communities, Annals of Botany, April 1952, NS16(2), 293-316.
- W R Cribb, Quantitative metallography of polyphase microstructures, Scripta Metallurgica, October 1978, 12(10), 893-898.
- FSMA Mirza, A statistical study of the structure of mixtures in particulate solids, PhD thesis, University of Exeter, 1970.
- Q F Li, R Smith and D G McCartney, Quantitative evaluation of fiber distributions in a continuously reinforced aluminium alloy using automatic image analysis, Materials Characterization, 1992, 28(4), 189-203.
- D Short and J Summerscales, The definition of microstructures in hybrid reinforced plastics, 5th International Conference of the European Chapter of SAMPE, Montreux ~ Switzerland, 12-14 June 1984, volume 2, paper 19.
- S-W Cheng, TK Dey and J Shewchuk, Delaunay Mesh Generation, Chapman & Hall/CRC Press/Taylor & Francis Group, Boca Raton FL, 2012. ISBN 978-1-58488730-0.
- DR Mulligan, SL Ogin, PA Smith, GM Wells and CM Worrall, Fibre-bundling in a short-fibre composite, Composites Science and Technology, 2003, 63(5), 715-725.
- PJ Davy and FJ Guild, The distribution of interparticle distance and its application in finite element modelling of composite materials, Proceedings of the Royal Society of London, 8 July 1988, 418(1854), 95-112.
- C Baley, A Le Duigou, A Bourmaud, P Davies, M Nardin and C Morvan, Reinforcement of polymers by flax fibers: role of interfaces, Chapter 6 in W Smitthipong, R Chollakup and M Nardin (editors), Bio-Based Composites For High-Performance Materials: from strategy to industrial application, CRC Press, Boca Raton FL, 2015, pp 87-112. ISBN 978-1-4822-1448-2.
- J Varghese and J Whitcomb, Effective properties of composites whose reinforcement has microstructure,
Mechanics of Advanced Materials and Structures, July 2006, 13(3), 227-235.
- B Thorfinnson and TF Biermann, Control and measurement of prepreg impregnation for elimination of voids in composite parts, 8th International Conference, SAMPE Europe, La Baule - France, 18-21 May 1987. Elsevier, Amsterdam, 1987, 159-171. ISBN 0-444-42803-8.
- NCW Judd and WW Wright, Voids and their effects on the mechanical properties of composites - an appraisal, SAMPE Journal, January/February 1978, 14(1), 10-14.
- SR Ghiorse, Effect of void content on the mechanical properties of carbon/epoxy laminates, SAMPE Quarterly, January 1993, 24(2), 54-59.
- C Baley, P Davies and D Cartié, Porosity in ocean racing yacht composites: a review, Applied Composite Materials, February 2015, 22(1), 13-28.
- X Liu and FA Chen, A review of void formation and its effects on the mechanical performance of carbon fiber reinforced plastic, Engineering Transactions, 2016, 64(1), 33-51.
- M Mehdikhani, L Gorbatikh, I Verpoest and SV Lomov, Voids in fiber-reinforced polymer composites: a review on their formation, characteristics, and effects on mechanical performance, Journal of Composite Materials, 2019, 53(12), 1579-1669.
- D Purslow, On the optical assessment of the void content in composite materials, Composites, 1984, 15(3), 207-210.
- DEW Stone and B Clarke, Ultrasonic attenuation as a measure of void content in carbon-fibre reinforced plastics, Non-Destructive Testing, 1975, 8(3),
137-145.
- G Mayr, B Plank, J Sekelja and G Hendorfer, Active thermography as a quantitative method for non-destructive evaluation of porous carbon fibre reinforced polymers, NDT&E International, 2011, 44(7), 537-543.
- JE Little, X Yuan and MI Jones, Characterisation of
voids in fibre reinforced composite materials, NDT&E International, March 2012, 46(1), 122-127.
- K-B Kim, DK Hsu and DJ Barnard, Estimation of porosity content of composite materials by applying discrete wavelet transform to ultrasonic backscattered signal, NDT&E International, new article in press.
- C Baley, M Lan, P Davies and D Cartié, Porosity in ocean racing yacht composites: a review, Applied Composite Materials, online 03 May 2014.
- B Madsen, A Thygesen and H Lilholt, Plant fibre composites - porosity and volumetric interaction, Composites Science and Technology, 2007, 67(7-8), 1584-1600.
Click here for TalisList |
Hot-linked references may only return an
abstract, which will allow you to judge the relevance of the paper to your
work.
Should you need to login to access the full publication, then it is
recommended that you use TalisList with Athens authentication. |
Return to MATS 347 home page
Updated by John Summerscales on
06-Oct-2023 16:16. Terms and conditions. Errors and omissions. Corrections.