Composites Engineering is a core module for "with composites engineering as a specialist pathway" available to students on BEng/MEng (honours) Mechanical Engineering (UCAS codes are H300 (BEng)/H304 (MEng)) or BEng/MEng (honours) Marine Technology courses (UCAS codes are J610 (BEng)/J612 (MEng)). The modules MATS 347, MATS 348 and MFRG 311 are the specific components of the pathway.
This module integrates the learning from the Composites Design and Manufacture ..and.. Quality Management II modules in a practical assignment to specify, design, manufacture, test and report on a prototype composite component.
University of Plymouth Module Record for MATS 348 (September 2023):
assessment is 0% examination and 100% coursework (module record only available with University of Plymouth login credentials).
- Design
- How to write a Product Design Specification
- DESIGN CHECKLIST based on KD Potter, Design of Composite Products - a personal viewpoint,
Composites Manufacturing, 1992, 3(3), 173-182. MooDLE.
- BS 7373-1:2001 Guide to the preparation of specifications. Guide to preparation.
- BS 7373-2:2001 Product specifications. Guide to identifying criteria for a product specification and to declaring product conformity
- BS 7373-3:2005 Product specifications. Guide to identifying criteria for specifying a service offering
- Safety factors
- Recommended reading for design
- DM Anderson, Design for manufacturability (including The Rule of 10), 2018.
- AT Mengistu, M Dieste, R Panizzolo and S Biazzo, Sustainable product design factors: a comprehensive analysis, Journal of Cleaner Production, 15 July 2024, 463, 142260.
- Costs
The components considered in this module (and the earlier modules MATS320 during 2001-2015 or MATS304 Composite Applications until AY2000/2001) were:
Academic Year | Components |
1997-98 | mountain bike suspension arm |
1998-99 | bicycle front forks |
1999-00 | yacht winch handle |
2000-01 | skaters trolley |
2001-02 | launching trolley for a dinghy |
2002-03 | man-portable bridge |
2003-04 | in-situ repair of a welded T-joint in an oiltank |
2004-05 | yacht mast spreader |
2005-06 | a crutch for a disabled table-tennis player |
2006-07 | (a) car spoiler, (b) cross bow limb (published in
Composites Part B: Engineering) |
2007-08 | legs for a bipedal robot |
2008-09 | kite-surf board |
2009-10 | (a/b) bicycle crank, (c) luge board |
2010-11 | (a) gas turbine blade, (b) ice-axe handle, (c) recreational helmet. |
2011-12 | bridge span of 584 mm with 100 mm square maximum cross-section. |
2012-13 | a torsion rod or a torsion tube |
2013-14 |
(a) bicycle sprocket, (b) in-wheel bicycle suspension, (c) coil over-spring (photos below table) |
2014-15 | composite car jack for motorsport |
2015-16 | wheel bracket for the Project Nevada hand-cycle |
2016-17 | (a) motor cycle front foot rest, (b) ice axe shaft, (c) BMX brake calliper, (d) arctic tow hook. |
2017-18 |
(a) cycle brake lever, (b) long board truck bar, (c) subsea locking mechanism |
2018-19 | (a) mountain bike handlebars, (b) bicycle wheel, (c) motorcycle swing arm, (d) blade (short ski), (e) carabiner, (f) truck lift crane arm |
2019-20 (Covid) |
(a) bicycle saddle, (b) welders head protection, (c) D-link winch hooking mechanism, (d) emergency services sledgehammer. |
2020-21 (Covid) |
(a) shin brace, (b) aircraft footstep, (c) Pulaski axe, (d) domestic hydro-turbine blade. (e) tennis racket, (f) helicopter blade attachment. |
2021-22 |
(a) lifeboat steering wheel, (b) stakeboard truck, (c) carabiner. |
2022-23 |
(a) wire strike, (b) drone blade, (c) cyclic control stick, (d) ice axe,
(e) nunchucks, (f) wind turbine blade, (g) dinghy rudder. |
2023-24 |
(a) yacht pad eye, (b) in-line load cell, (c) marine propeller blade, (d) surf fin. |
2024-25 | (a) lifting bar, (b) bicycle crank arm, (c) golf driver, (d) gear change paddle, (e) hydrofoil,
(f) bell crank, (g) tail rotor blade, (h) landing gear torque arm, (i) J80 tiller |
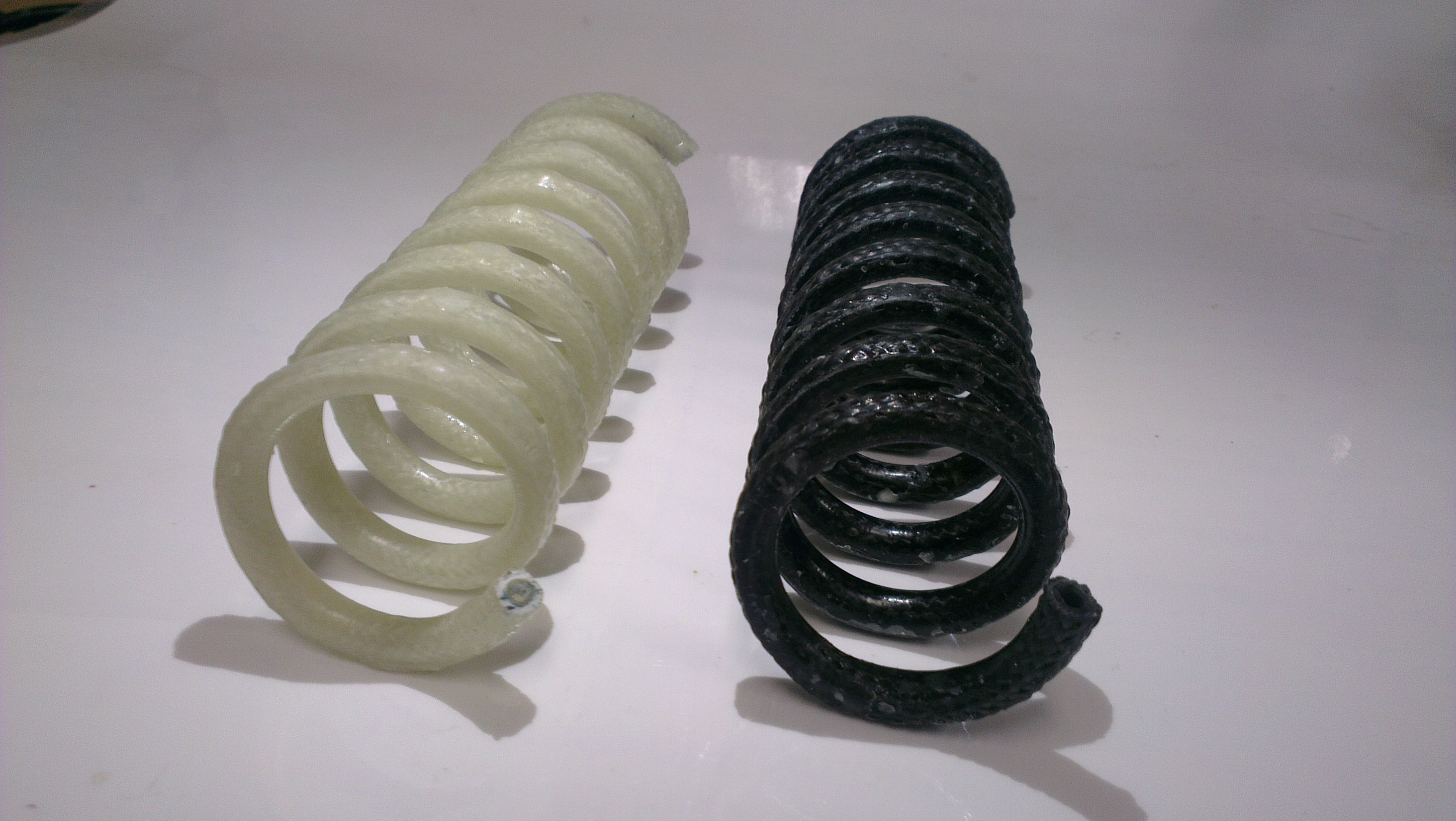
2013/14c photographs courtesy of Mathew Brierley
Factlets:
- Alain Giocosa (Renault Guyancourt) in a Keynote Address (FPCM-8, Douai - France, 13 July 2006) suggested that each 100 kg saved in a passenger car translates to a fuel saving of 4 litres/1000 km.
- Costas Soutis (University of Sheffield) in Plastics, Rubber and Composites, 2009, 38(9/10), 359-366 states that "1 kg weight reduction saves over 2900L fuel per year" in the context of the Airbus A320.
- "Each kilogramme cut means a saving of roughly $1m (£603,000) in costs over the lifetime of an aircraft - and the use of [carbon fibre] composites can reduce the weight of an aircraft by up to 20%". Tim Bowler, Carbon fibre planes: Lighter and stronger by design, BBC News Business, 28 January 2014.
- Lightweight Composites: vital cog in the CO2 emission reduction blueprint, ICICI Securities Market Wrap, 09-13 February 2015.
Unlikely but true ...
Modelling sandwich structure in Solidworks
- You need to define a "contact set" to bond the two facesheets to the core manually [Maozhou Meng]
HEALTH & SAFETY
It is important that all students are aware of the Health and Safety considerations for this module. You will be required to attend the Health and Safety presentation and to sign to confirm that you have done so before you will be allowed to use the facilities in the ACMC laboratory (Brunel 007). This support material can be accessed
online.
SAFETY FACTORS
CONDITION | FACTOR | REFERENCE |
Static short-term loads (construction industry) | 2 | 1 |
Static long-term loads (construction industry) | 4 | 1 |
Variable/changing loads (construction industry) | 4 | 1 |
Repeated loads (construction industry) | 6 | 1 |
Fatigue or load-reversal (construction industry) | 6 | 1 |
Impact loads repeated (construction industry) | 10 | 1 |
Composite manufacture by handwork | 1.5 | 2 |
Composite manufacture by machine controlled spray application | 1.5 | 2 |
Composite manufacture by hand-held spray application | 3 | 2 |
Composite chemical pressure vessel with a thermoplastic liner | 1.2 | 2 |
Composite chemical pressure vessel without a thermoplastic liner | up to 2 | 2 |
Composite operating temperature (dependent on HDT) | 1.0-1.25 | 2 |
Composite post-cure to manufacturers specification | 1.1 | 2 |
Composite for operation up to 45ºC | 1.3 | 2 |
Composite for operation over 45ºC | 1.3 | 2 |
References
- SM Halliwell, Polymer composites in construction, Construction Research Communications Limited by permission of Building Research Establishment Limited, Watford/London, 2000. ISBN 1-86081-429-8. PU CSH Library.
- BS 4994:1987 Design and construction of vessels and tanks in reinforced plastics
Pugh's design specification elements (Pugh, 1991) |
Politics | Environment | Ergonomics | Aesthetics |
Legal | Patents | Standards specifications | Documentation |
Market constraints | Company constraints | Competition | Customer |
Size | Weight | Performance | Safety |
Maintenance | Life in service | Product life span | Shelf life storage |
Materials | Manufacturing facility | Product cost | Time scale |
Shipping | Packing | Installation | Disposal |
Processes | Testing | Quality | Quality reliability |
Reference
- S Pugh, Total design: integrated methods for successful product engineering, Addison-Wesley Publishing, Harlow - UK, 1991. PU CSH Library.
Recommended reading:
- MF Ashby, Materials Selection in Mechanical Design, Pergamon Press, Oxford, 1992. ISBN 0-08-041907-0. Fourth edition: ISBN ISBN 978-1-85617-663-7, 2011. PU CSH Library.
- D Gay, Composite Materials: Design and Applications - third edition, CRC Press, 2014. ISBN 978-1-4665-8487-7.
- RF Gibson, Principles of Composite Material Mechanics - 4th edition, CRC Press, 2016. ISBN 978-1-4987-2069-4.
- DC Smoot and AB Strong, Product and Process Innovation - a review, Journal of Advanced Materials, April 2006, 38(2), 64-79.
- A Brent Strong, Composites in Manufacturing - Case Studies, Society of Manufacturing Engineers, 1991. ISBN 0-87263-406-x. PU CSH Library
- JFV Vincent, OA Bogatyreva, NR Bogatyrev, A Bowyer and A-K Pahl, Biomimetics: its practice and theory, Journal of the Royal Society - Interface (online).
Supplementary materials: Appendix 1: Altshuller’s 40 Inventive Principles with biological examples Appendix 2: Apportioning Altshuller’s conflict features and inventive principles to the PRIZM categories. Appendix 3: Examples of functions at various size scales in biology and technology.
Cost comparisons
- Life cycle costing (review papers)
- MG Bader, Selection of composite materials and manufacturing routes for cost-effective performance, Composites Part A: Applied Science and Manufacturing, July 2002, 33(7), 913-934.
- SW Beckwith, Typical cost elements of composite stuctures manufacturing (Part 1 - program elements and recurring cost element), SAMPE Journal, September-October 2023, 59(5), 48-49.
- SW Beckwith, Typical cost elements of composite stuctures manufacturing (Part 2 - learning curve applications), SAMPE Journal, November-December 2023, 59(6), 60-61.
- P Bortolotti, D Berry, R Murray, E Gaertner, D Jenne, R Damiani, G Barter and K Dykes, A detailed wind turbine blade cost model, National Renewable Energy Laboratory (NREL) Technical Report NREL/TP-5000-73585, June 2019.
- M Cabrera-Ríos and JM Castro, The balance between durability, reliability and affordability in structural composites manufacturing, Polymer Composites, 2007, 28(2), 233-240.
- EA Calado, M Leite and A Silva, Selecting composite materials considering cost and environmental impact in the early phases of aircraft structure design, Journal of Cleaner Production, 10 June 2018, 186, 113-122.
- J Clarke, A McIlhagger, D Dixon, E Archer, G Stewart, R Brelsford and J Summerscales, A cost model for 3D woven preforms, Journal of Composites Science (Special Issue Characterization and Modelling of Composites, Volume II), 2022, 6(1), 18.
- B Crawford, D Tamaki and AS Milani, Cost modeling of the manufacture of a GFRP leisure boat hull for both open chopped spray moulding and resin infusion processes, Composites Research Network-Okanagan Node report CRNO-11082017-1, 28 August 2017.
- R Curran, S Raghunathan and M Price, Review of aerospace engineering cost modelling: the genetic causal approach, Progress in Aerospace Sciences, November 2004, 40(8), 487-534.
- L Dickinson, M Mohamed and B Lienhart, Cost modeling for 3D woven preforming process, International SAMPE Symposium "Bridging The Centuries", Long Beach CA, 21-25 May 2000, volume 45, pp 227-140.
- L Dickinson, M Salama and D Stobbe, Design approach for 3D woven composites: Cost vs. performance, International SAMPE Symposium "2001: A Materials and Processes Odyssey", Long Beach CA, 06-10 May 2001, volume 46, pp 765-778.
- E Fauster, C Schillfahrt, C Hueber and R Schledjewski, Automated profile preforming for structural components, Science and Engineering of Composite Materials, 2016, 24(5), 163-182.
- G Gardiner, Revolutionizing the cost paradigm,
Part 1 Feedstock,
Part 2 Forming, CompositesWorld, April 2020, 6(4), 36- 44 & May 2020, 6(5), 24-33.
- MK Hagnell and M Akermo, A composite cost model for the aeronautical industry: methodology and case study, Composites Part B: Engineering, 15 September 2015, 79, 254-261.
- K Horejsi, J Noisternig, O Koch and R Schledjewski, Cost-based process selection for CFRP aerospace parts, JEC Composites magazine, May-June 2013, (81). 60-62.
- Ch Hueber, K Horejsi and R Schledjewski, Review of cost estimation: methods and models for aerospace composite manufacturing, Advanced Manufacturing: Polymer and Composites Science, 2016, 2(1), 1-13.
- M Kaufmann, D Zenkert and C Mattei, Cost optimization of composite aircraft structures including variable laminate qualities, Composites Science and Technology, October 2008, 68(13), 2748-2754.
- SK Mazumdar, Cost Estimation, Chapter 11 in SK Mazumdar, Composites Manufacturing - materials, product and process engineering, CRC Press, Boca Raton FL, 2002. ISBN 0-8493-0585-3. PU CSH Library
- J Meredith, E Bilson, R Powe, E Collings and K Kirwan, A performance versus cost analysis of prepreg carbon fibre epoxy energy absorption structures, Composite Structures, June 2015, 124, 206-213.
- P Mårtensson, D Zenkert and M Åkermo, Effects of manufacturing constraints on the cost and weight efficiency of integral and differential automotive composite structures, Composite Structures, 15 December 2015, 134, 572-578.
- JD Russell, Composites Affordability Initiative: successes, failures - where do we go from here?, SAMPE Journal, March/April 2007, 43(2), 26-36.
- A Sohouli, M Yildiz and A Suleman, Cost analysis of variable stiffness composite structures with application to a wind turbine blade, Composite Structures, 1 November 2018, 203, 681-695.
- TA Turner, LT Harper, NA Warrior and CD Rudd, Low-cost carbon-fibre-based automotive body panel systems: a performance and manufacturing cost comparison,
Proceedings of the Institution of Mechanical Engineers, Part D: Journal of Automobile Engineering, 2008, 222(1), 53-63.
- WJC Verhagen, PB Garcia, P Mariot, J-P Cotton, D Ruiz, R Redon and R Curran, Knowledge-based cost modelling of composite wing structures, International Journal of Computer Integrated Manufacturing, 2012, 25(4-5), 368-383.
- J Verrey, MD Wakeman, V Michaud, J-AE Månson, Manufacturing cost comparison of thermoplastic and thermoset RTM for an automotive floor pan, Composites Part A: Applied Science and Manufacturing, January 2006, 37(1), 9-22.
- A Vita, V Castorani, M Germani and M Marconi, Comparative life cycle assessment and cost analysis of autoclave and pressure bag molding for producing CFRP components, The International Journal of Advanced Manufacturing Technology, December 2019, 105, 1967–1982.
- F Weiland, C Weimer, F Dumont, ChV Katsiropoulos, SpG Pantelakis, I Sitaras, AA Skordos, E Berthe, P de Luca, Process and cost modelling applied to manufacture of complex aerospace composite part, Plastics, Rubber and Composites, December 2013, 42(10), 427-436.
- J Zeilon, Cost-effective manufacturing systems for composite parts, JEC Composites magazine, July 2013, (82), 28-29.
- K Zimmermann, Cost and weight analysis of ultra thick laminates for compact landing gear fitting, Plastics, Rubber and Composites: Macromolecular Engineering, May 2013, 42(4), 137-143(7).
Environmental assessments
- BA Ahmed Ali, SM Sapuan, ES Zainudin and M Othman, Implementation of the expert decision system for environmental assessment in composite materials selection for automotive components, Journal of Cleaner Production, 16 November 2015, 107, 557-567.
- M Akhshik, S Panthapulakkal, J Tjong and M Sain, The effect of lightweighting on greenhouse gas emissions and life cycle energy for automotive composite parts,
Clean Technologies and Environmental Policy, 24 January 2019, FirstOnline.
- M Raugei, D Morrey, A Hutchinson and P Winfield, A coherent life cycle assessment of a range of lightweighting strategies for compact vehicles, Journal of Cleaner Production, 1 December 2015, 108, 1168-1176.
|
|