Concern for environmental issues is not a new phenomenon: key dates ..and.. definitions of eco-efficiency.
A key political concept in this context is Sustainability and a major tool is Life Cycle
Assessment/Analysis (LCA).
A major business tool is Environmental Management Systems, especially ISO 14001.
EuCIA have launched a Eco Impact Calculator to provide an easy way to calculate the environmental impacts of composite products from “cradle to gate”.
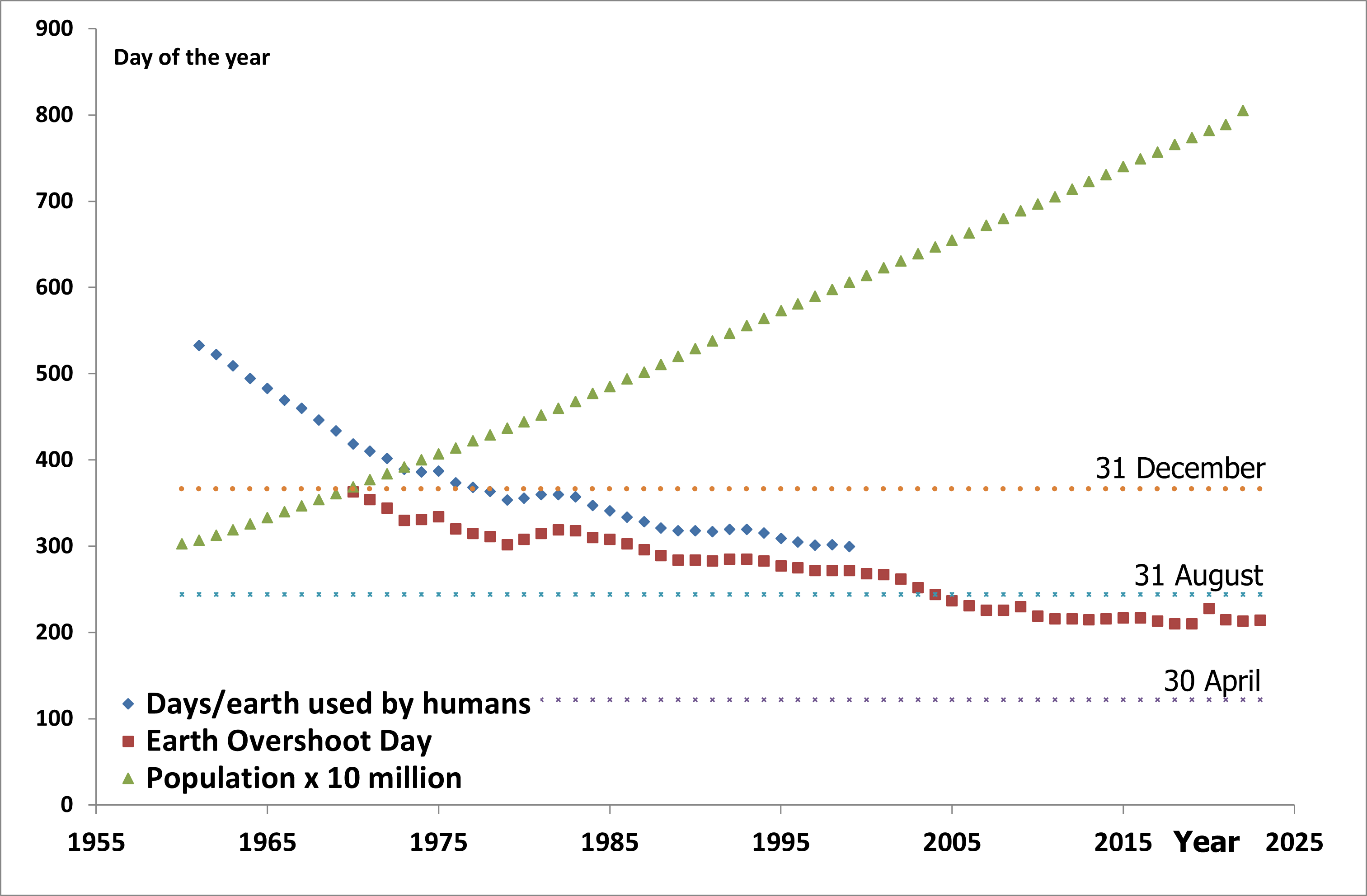
Figure 1: Earth Overshoot Day vs population of the planet.
"Earth Overshoot Day is computed by dividing the planet’s biocapacity (the amount of ecological resources Earth is able to generate that year), by humanity’s Ecological Footprint (humanity’s demand for that year), and multiplying by 365, the number of days in a year".
Wesley Stephenson, All the plastic you can and cannot recycle, BBC News Science and Environment, 21 September 2018.
Table 1 presents some data on the tonnage of materials produced or consumed each year:
Table 1: Annual consumption data for key materials
Material |
Total World Annual Production/Consumption |
Census date |
Reference |
Steel |
1107.1 million tonnes (MT) |
2005 |
World
Steel Review - 2006, accessed 27 February 2006. |
Aluminium |
23.423 million metric tonnes |
2005 |
Primary
Aluminium Production, accessed 27 February 2006. |
Copper |
12.4 million tonnes |
2003 |
Joël PT Kapusta,
JOM World Nonferrous Smelters Survey, Part I: Copper, July 2004. |
Zinc |
>10 million metric tonnes |
2005 |
Sucden,
Metals - Base and
Precious, accessed 27 February 2006. |
Timber |
EU-25: 21.8 MT#
(industrial roundwood) |
2003 |
E. Mäki-Simola & Imola Panagopoulos,
The production of wood and forest industry products in EU-25, 4 October 2005. |
Timber |
UK: 7.5 MT# (supplied from
Britain’s forests) |
2004 |
Forestry Commission,
Timber Statistics,
18 January 2006. |
Plastics |
100 million tonnes |
"today" |
Plastics
recycling information sheet, Waste Online, February 2006. |
Plastics |
UK: 4.7 million tonnes |
2002 |
Introduction
to plastics, British Plastics Federation, 2003. |
Composites |
Western Europe: 1.54 million tonnes |
2000 (estimate) |
UK
Polymer Composites Sector Foresight Study and Competitive Analysis,
October 2001. |
Composites |
UK: 0.21 million tonnes |
2000 (estimate) |
UK
Polymer Composites Sector Foresight Study and Competitive Analysis,
October 2001. |
# The conversion factor used for this data was the figure for wood
of 1000 metric tonnes = 1480 cubic meters [1].
Analyses of the composition of municipal solid waste (MSW)
are available for the United States of America [2] and the principality of Wales
[3]. The US
Environmental Protection Agency (EPA) defines MSW to include durable goods,
containers and packaging, food wastes, yard wastes, and miscellaneous inorganic
wastes from residential, commercial, institutional, and industrial sources.
EPA excludes industrial waste, agricultural waste, sewage sludge and all
categories of hazardous wastes (the latter including batteries and medical
wastes). The proportion of plastics in MSW in each case was 9.5% and up to
11% respectively.
Figure 2: The growth of the reinforced plastics market in the USA.
Figure 1 shows the growth of the market for reinforced plastics.
The data up to 1996 is from the Society for the Plastics Industry with the more recent data from the American
Composites Manufacturers Association (e.g.
US market statistics for 2005 [4]). Note that in spite of the apparent discontinuity in sector sizes between 1996 and 1997 due to reallocation
of categories, the total market figures appear to follow a sensible trend.
At the design state of any product do
consider the possibility of re-use and, if that is not practical, do design for dis-assembly or recycling.
Any (re-)processing of materials will require energy. That
raises issues of collection and transport, fuel efficiency and the ethics of
global sourcing. Unnecessary use of energy costs money and potentially
contributes to climate change. A European project,
RECIPE: Reduced Energy Consumption In
Plastics Engineering, aims to help the plastics processing industry to
reduce their energy consumption. The RECIPE best practice guide [5]
provides a structured and practical approach to improving energy efficiency in
the processing of plastics.
Article 4 of the revised EU Waste Framework Directive [6] sets out five steps for dealing with waste, ranked according to environmental impact - the waste hierarchy (Columns 1 and 2 of Table 1 [7]).
Table 2: Recycling and disposal options for polymer matrix composites (URL for Table)
The BBC website presents "Seven charts that explain the plastic pollution problem".
The potential routes for dealing with waste composites are summarised in Figure 3.
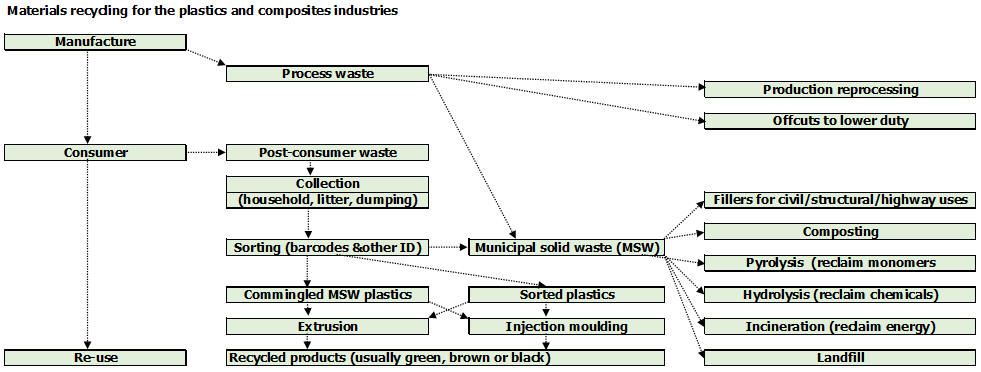
Figure 3: The options for end-of-life composites
A list of review papers on recycling composites can be found here. Halliwell [8] has recently produced an excellent best practice guide on
End-Of-Life options for composite waste. Liu et al [9] have reported an eco-audit comparison for end-of-life wind turbine blades.
There is increasing interest in reclamation of high-value materials.
In particular, technologies for the recovery of short carbon fibres are being
developed [10].
Carbon Fibre Reinforced Plastics (CFRP) recycling
- C-W Liu, W-J Hong, B-T Yang, C-W Lin, L-C Wang and C-C Chen, Switchable deep eutectic solvents as efficient and sustainable recycling media for carbon fiber reinforced polymer composite waste, Journal of Cleaner Production, 10 December 2022, 378, 134334.
- K Kawajiri and M Kobayashi, Cradle-to-Gate life cycle assessment of recycling processes for carbon fibers: a case study of ex-ante life cycle assessment for commercially feasible pyrolysis and solvolysis approaches, Journal of Cleaner Production, 10 December 2022, 378, 134581.
Abandoned and Derelict Vessels (ADV) End-of-Life (EoL) fibreglass boats ~ videos
Composting
One alternative for bio-based materials (natural fibres and plant-based resins)
is disposal by composting. Hermann et al [10] classify "composting" into four categories as shown in Table 3 where chemical/mechanical pulp is for paper and cellulose production (and
hence probably appropriate for natural fibres). Specific benefits of
compost [11] are that:
- compost stores carbon in the soil,
- nitrogen contained in compost is an organic fertiliser,
- compost used as a soil conditioner improves the soil structure,
- compost used as a soil conditioner reduces fossil emissions arising from the use of peat.
Table 3: Four types of biological waste treatment (after Hermann et al [11])
| bacteria (no fungi) | Anaerobic digestor | |
Aerobic composting |
bacteria and fungi |
temperature: 50-60°C | chemical pulp - starch - starch/PCL- PHA - PLA |
thermophilic digestion | | industrial composting | chemical pulp - mechanical pulp - starch - starch/PCL - PBAT -PHA - PLA |
temperature: ≤35°C | chemical pulp - starch - starch/PCL- PHA | mesophilic digestion | | home composting | chemical pulp - mechanical pulp - starch - starch/PCL - PBAT -PHA |
outputs | CO2 - humus | digestate | | compost | CO2 - CH4 - N2O - humus |
There are essentially two options (a) aerobic: carried out either in open air windrows or in enclosed vessels, or (b) anaerobic: required when animal by-products or catering wastes are included [12]. A typical value for mass loss during composting (for grassland in Austria) is 56% [13]. A demonstration-scale anaerobic digestion (AD) plant is operating at Dufferin (Toronto) solid waste transfer station with a mass balance (based on 100 metric tons/day) of 50% biogas and effluent, 25% digestate and 25% residue [14]. The biogas varies due to the batch operation but is typically 110 m3/metric ton with an average of 56% methane (ranges from 45-73%) by volume. Jana et al [15] suggest that the biogas is typically 60-65% methane,
35% carbon dioxide and a small amount of other impurities". Similarly, "pure landfill gas can contain up to 35% carbon dioxide, 65% methane and no oxygen" [16]. Further resources include BioCycle magazine and the Composting Association.
Life Cycle Assessment (LCA) studies have suggested that composting is preferable to incineration when the compost is used to enhance the carbon content of agricultural soils [11, 17].
A biodegradable material is expected to reach a defined extent of degradation by
biological activity under specific environmental conditions within a given time under standard test conditions [18]. Krzan et al [19] have recently reviewed the standards and certification
appropriate to environmentally degradable plastics.
The biodegradation of a polymeric materials under controlled composting conditions is the subject of a number of standard methods, including:
- ASTM D5338-15(2021): Standard Test Method for Determining Aerobic Biodegradation of Plastic Materials Under Controlled Composting Conditions, incorporating thermophilic temperatures [20].
- ASTM 6002-96(2002) Standard Guide for Assessing the Compostability of Environmentally Degradable Plastics (Withdrawn 2011 with no replacement) [21].
- ASTM 6340-98(2007) Standard Test Methods for Determining Aerobic Biodegradation of Radiolabeled Plastic Materials in an Aqueous or Compost Environment (withdrawn 2016 with no replacement) [22].
- ASTM D6400-23: Standard Specification for Labeling of Plastics Designed to be Aerobically Composted in Municipal or Industrial Facilities [23].
- ASTM D6868-21: Standard Specification for Labeling of End Items that Incorporate Plastics and Polymers as Coatings or Additives with Paper and Other Substrates Designed to be Aerobically Composted in Municipal or Industrial Facilities [24].
- ISO 14851:2019 Determination of the ultimate aerobic biodegradability of plastic materials in an aqueous medium — Method by measuring the oxygen demand in a closed respirometer [25].
- ISO 14852:2001 Determination of the ultimate aerobic biodegradability of plastic materials in an aqueous medium - Method by analysis of evolved carbon dioxide [26].
- ISO 14853:2016 Plastics — Determination of the ultimate anaerobic biodegradation of plastic materials in an aqueous system — Method by measurement of biogas production [27].
- ISO 14855-1:2005 Determination of the ultimate aerobic biodegradability of plastic materials under controlled composting conditions — Method by analysis of evolved carbon dioxide — Part 1: General method [28].
- ISO 14855-2:2018 Determination of the ultimate aerobic biodegradability of plastic materials under controlled composting conditions — Method by analysis of evolved carbon dioxide — Part 2: Gravimetric measurement of carbon dioxide evolved in a laboratory-scale test [29].
- ISO 16929:2021 Plastics — Determination of the degree of disintegration of plastic materials under defined composting conditions in a pilot-scale test [30].
The EU Directive on Packaging and Packaging Waste (94/62/EC) criteria for biodegradability are set out in BS EN 13432 [31] while the criteria in North America are set out in ASTM D6400 [23]. The requirements of the standard include:
- biodegradation: over 90% relative to the standard (cellulose) in 180 days under conditions of controlled composting using respirometric methods (ISO14855) [28, 29],
- disintegration: over 90% in 3 months (ISO16929) [30],
- ecotoxicity: test results for aquatic and terrestrial organisms (Daphnia magna, worm test, germination test) as for reference compost,
- absence of hazardous chemicals (included in a reference list).
Organisms that possess cellulase (the enzyme which cleaves sugar from the cellulose
molecule) include bacteria, some flagellate and ciliate protozoa, and fungi [32]. If an animal is to digest cellulose, it must enter into an alliance with such an organism. For example, termites have a symbiotic relationship with fungi which provides the symbionts with a rich source of cellulose for food in return for access to glucose cleaved from the cellulose and additionally to protein, vitamins and essential amino-acids produced by the fungi. Termites hatch without this essential intestinal flora and are inoculated with it by being fed faeces and regurgitant that contain the symbionts. The fungal deterioration of cellulosic textiles has been reviewed by Montegut et al [33].
Milner et al [34, 35] have reported a new strain of thermophylic bacteria that can break down cellulose waste to produce useful renewable fuels for the transport industry. The Geobacillus family normally synthesise sugars and produce lactic acid as a by-product when they break down biomass in a compost heap. The re-engineered TM242 strain is claimed to produce ethanol more efficiently (yields of 10 to 15%) and cheaply than in traditional yeast-based fermentation.
Gómez and Michel [36] investigated the relative biodegradability of a range of polymeric materials and natural fiber composites under composting, soil incubation and anaerobic digestion conditions. The validity of the tests was confirmed in that positive controls (cellulose paper) biodegraded by more than 70% in all three systems in a reproducible manner. While some of the bio-based plastics and natural fibers biodegraded to an appreciable extent, plastics containing additives that supposedly confer biodegradability to polymers such as polyethylene and polypropylene did not improve the biodegradability of the polymers. SEM analysis confirmed that substantial biodegradation of polyhydroxyalkanoate-based (PHA) plastics occurred and that some surface changes occurred in co-polyester/corn-based plastic and coconut coir materials. However, SEM confirmed that no degradation of polypropylene and polyethylene occurred, even after amendment with additives meant to confer biodegradability. The relative biodegradability of the materials during long-term soil incubation was PHA>co-polyester/corn-based plastic>composted cow manure>plastarch>paper pulps>natural fibers>conventional plastics containing additives to enhance biodegradability = conventional plastics.
Evagelisti et al [37] investigated the environmental impact of the organic fraction of municipal solid waste (OFMSW) treatment in London. The Life Cycle Assessment (LCA) included sensitivity analysis to test the robustness of the model.
Environmental impact classification factors
Azapagic has presented an analysis which permits the quantification of environmental impact classification factors. Any (re-)processing of materials will require energy.
The discipline of biomimetics, may have much to teach us here. Biological systems create wastes which are raw materials for other plants and/or animals. For an insight into how complex natural systems can evolve, see the life cycle of Maculinea Arion (large blue butterfly) and its dependence on Myrmica Sabuleti (red ant).
References:
- B Michie and P Wardle, EFI/WFSE Trade Flow Database, European Forest Institute, Joensuu - Finland, 2000, updated 2002.
- Municipal Solid Waste Profile, 16 April 1997.
- The Composition of Municipal Solid Waste in Wales, December 2003.
- Composites Industry Statistics, American Composites Manufacturers Association, 2006.
- Best Practice Guide for Low Energy Plastics Processing from the European Community funded RECIPE project (supported by the Intelligent Energy Europe programme) contract no. EIE/04/153/S07.38646.
- S Halliwell, End of Life options for composite waste - recycle, reuse or dispose?, National Composites Network Best Practice Guide, 2006. MooDLE. (NCN registrants can download the guide from NCN Best Practice Guide - Composites recycling guide).
- Directive 2008/98/EC on waste (Waste Framework Directive), accessed on 06 June 2014.
- Waste legislation and regulations, accessed on 06 June 2014.
- P Liu, F Meng and CY Barlow, Wind turbine blade end-of-life options: an eco-audit comparison, Journal of Cleaner Production, 1 March 2019, 212, 1268-1281.
- R Mehta, A lifeline for waste carbon fibres, Materials World, January 2010, 18(1), 6-7.
- BG Hermann, L Debeer, B de Wilde, K Blok and MK Patel, To compost or not to compost: carbon and energy footprints of biodegradable materials’ waste treatment, Polymer Degradation and Stability, June 2011, 96(6), 1159-1171.
- Jeremy Jacobs, The Compositing Association, private communication (e-mail), Monday 26 June 2006 08:45
- M Narodoslawsky and A Niederl, Chapter 10: The Sustainable
Process Index (SPI), pp 159-172 in Jo Dewulf and Herman van Langenhove (editors),
Renewables-Based Technology: Sustainability Assessment, Wiley, Chichester, 2006. ISBN 978-0-470-02241-2. PU CSH Library.
- N Goldstein, Source separated organics as feedstock for digesters, BioCycle, August 2005, 46(8), 42.
- S Jana, NR Chakrabarty and SC Sarkar, Removal of Carbon Dioxide from Biogas for Methane Generation, Journal of Energy in Southern Africa, August 2001, 12(3), 412-414.
- L Greenham and P Walsh, Carbon Dioxide Detectors For Health & Safety Applications, Petro Industry News, December 2004, pp 34-35 (page no longer available).
- HH Khoo, RBH Tan and KWL Chng, Environmental impacts of conventional plastic and bio-based carrier bags - Part 1: Life cycle production, International Journal of Life Cycle Assessment, 2010, 15(3), 284-293.
- Richard Murphy and Ian Bartle, Biodegradable Polymers and Sustainability: Insights from Life Cycle Assessment, Summary Report presented at the National Non-Food Crops Centre seminar, London, 25 May 25 2004.
- Andrej Krzan, S Hemjinda, S Miertus, A Corti and E Chiellini, Standardization and certification in the area of environmentally degradable plastics, Polymer Degradation and Stability, December 2006, 91(12), 2819-2833.
- ASTM D5338-15(2021): Standard Test Method for Determining Aerobic Biodegradation of Plastic Materials Under Controlled Composting Conditions, incorporating thermophilic temperatures.
- ASTM 6002-96(2002) Standard Guide for Assessing the Compostability of Environmentally Degradable Plastics (Withdrawn 2011 with no replacement).
- ASTM 6340-98(2007) Standard Test Methods for Determining Aerobic Biodegradation of Radiolabeled Plastic Materials in an Aqueous or Compost Environment (withdrawn 2016 with no replacement).
- ASTM D6400-23: Standard Specification for Labeling of Plastics Designed to be Aerobically Composted in Municipal or Industrial Facilities.
- ASTM D6868-21: Standard Specification for Labeling of End Items that Incorporate Plastics and Polymers as Coatings or Additives with Paper and Other Substrates Designed to be Aerobically Composted in Municipal or Industrial Facilities.
- ISO 14851:2019 Determination of the ultimate aerobic biodegradability of plastic materials in an aqueous medium - Method by measuring the oxygen demand in a closed respirometer.
- ISO 14852:2001 Determination of the ultimate aerobic biodegradability of plastic materials in an aqueous medium - Method by analysis of evolved carbon dioxide.
- ISO 14853:2016 Plastics - Determination of the ultimate anaerobic biodegradation of plastic materials in an aqueous system - Method by measurement of biogas production.
- ISO 14855-1:2005 Determination of the ultimate aerobic biodegradability of plastic materials under controlled composting conditions - Method by analysis of evolved carbon dioxide - Part 1: General method.
- ISO 14855-2:2018 Determination of the ultimate aerobic biodegradability of plastic materials under controlled composting conditions - Method by analysis of evolved carbon dioxide - Part 2: Gravimetric measurement of carbon dioxide evolved in a laboratory-scale test.
- ISO 16929:2021 Plastics - Determination of the degree of disintegration of plastic materials under defined composting conditions in a pilot-scale test [30].
- BS EN 13432:2000 Packaging. Requirements for packaging recoverable through composting and biodegradation. Test scheme and evaluation criteria for the final acceptance of packaging.
- J Scott Turner, The Extended Organism: The Physiology of Animal-built Structures, Harvard University Press, September 2002. ISBN 0-674-00985-1. PU CSH Library.
- D Montegut, N Indictor and RJ Koestler, Fungal deterioration of cellulosic textiles: a review, International Biodeterioration, 1991, 28(1-4), 209-226.
- P Milner, SM Martin, KL Eley, R Cripps, E Firth, C Mercier, J Robinson and T Atkinson, Development of a second generation bioethanol process using TM242 – a thermophilic bacillus, Autumn Meeting, Society for General Microbiology, Trinity College Dublin, 08-11 September 2008, abstracts book page 23.
- Compost heap bacteria could help produce renewable fuel, BioTech International, September 2008, 20(4), 26.
- EF Gómez, and FC Michel, Biodegradability of conventional and bio-based plastics and natural fiber composites during composting, anaerobic digestion and long-term soil incubation, Polymer Degradation and Stability, December 2013, 98(12), 2583-2591.
- S Evangelisti, P Lettieri, D Borello and R Clift, Life cycle assessment of energy from waste via anaerobic digestion: A UK case study, Waste Management, January 2014, 34(1), 226-237.
Further reading:
- B Adhikari, D De and S Maiti, Reclamation and recycling of waste rubber, Progress in Polymer Science , 2000, 25(7), 909-948.
- Adisa Azapagic, Alan Emsley and Ian Hamerton, Polymers: The Environment and Sustainable Development,
John Wiley & Sons, March 2003, ISBN 0 471 87741 7 (1st edition soft-cover). PU CSH Library
- Caroline Baillie, Green Composites: polymer composites and the
environment,
Woodhead Publishing Limited, Cambridge, 2004.
ISBN 1-85573-739-6. CRC Press LLC, Boca Raton FL, 2004. ISBN
0-8493-2576-5. PU CSH Library
- Jack Harris, Material matters: availability of uranium, Materials World,
January 2006, 14(1), 56.
- L Henry, A Schneller, J Doerfler, WM Mueller, C Aymonier and S Horn, Semi-continuous flow recycling method for carbon fibre reinforced thermoset polymers by near- and supercritical solvolysis, Polymer Degradation and Stability, November 2016, 133, 264-274.
- J Howarth, SSR Mareddy and PT Mativenga, Energy intensity and environmental analysis of mechanical recycling of carbon fibre composite, Journal of Cleaner Production, 15 October 2014, 81, 46-50.
- Y Leterrier, Life Cycle Engineering of Composites, Comprehensive
Composite Materials Volume 2: Polymer Matrix Composites, Elsevier, 2000,
1073-1102.
ISBN 0-08-043720-6.
- X Li, R Bai and J McKechnie, Environmental and financial performance of mechanical recycling of carbon fibre reinforced polymers and comparison with conventional disposal routes, Journal of Cleaner Production, 20 July 2016, 127, 451-460.
- James Lovelock, The Revenge of Gaia: why the Earth is fighting back – and
how we can still save humanity, Allen Lane, London, 2006.
ISBN-13:
978-0-713-99914-3. PU CSH Library
- TJ O'Neill, Life Cycle Assessment of Environmental Impact of Polymeric Products, Rapra Review Reports, 2003, 13(12), 1-133. ISBN 1-85957-364-9. PU CSH Library
- Steve Pickering and Peter Hornsby, Polymer Composites: recycling and
energy recovery, Materials World, September 1995, 3(9), 426-427.
- J Rybicka, A Tiwari, PA Del Campo and J Howarth, Capturing composites manufacturing waste flows through process mapping, Journal of Cleaner Production, 15 March 2015, 91, 251-261.
- Gerald Scott, Polymers and the Environment, Royal Society of Chemistry,
Cambridge, 1999. ISBN 0-85404-578-3. PU CSH Library
- B.A. Ahmed Ali, S.M. Sapuan, E.S. Zainudin, M. Othman,
Implementation of the expert decision system for environmental assessment in composite materials selection for automotive components,
Journal of Cleaner Production, 16 November 2015, 107, 557-567.
Conventional materials selection system was replaced with sophisticated software tools by rapid changing technology. The growing environmental concerns and regulations widely among the industry, especially in automobiles, force us to explore the natural fiber materials as a replacement for synthetic materials which is in common use. As a result of extensive research and development, new natural fiber reinforced composite materials are emerging and the database of materials growing exponentially. The decision of selecting optimized materials was complicated, as it involves diversified choice of materials, coupled with various influencing criteria for the selection process. To abstain from deciding inappropriate materials, the technology of expert system software tools can help us in the appropriate materials selection. The objective of this research was to explore the implementation of Analytical Hierarchy Process (AHP) using the expert choice software tool for deciding optimum natural fiber reinforced composite materials by considering main criteria and sub-criteria in the hierarchical model. The final judgement was performed with different scenarios of sensitivity analysis, giving priority to the environmental factors and sustainability. The result shows that the natural fiber composite material hemp and polypropylene gained the higher rank in the selection process and almost compliant with the requirements of industrial product design specification and can be recommended to automotive component manufacturers to enforce green technology.
Composting polymers:
- CA Ryan, SL Billington and CS Criddle, Methodology to assess end-of-life anaerobic biodegradation kinetics and methane production potential for composite materials, Composites Part A: Applied Science and Manufacturing, April 2017, 95, 388–399.
- E Castro-Aguirre, R Auras, S Selke, M Rubino and T Marsh, Insights on the aerobic biodegradation of polymers by analysis of evolved carbon dioxide in simulated composting conditions, Polymer Degradation and Stability, March 2017, 137, 251–271.
Other resources:
Composites recycling companies
Return to MATS 347 home page
Updated by John Summerscales on
28-Jul-2025 11:53. Terms and conditions. Errors and omissions. Corrections.